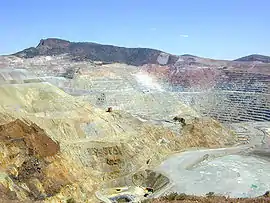

Copper extraction refers to the methods used to obtain copper from its ores. The conversion of copper ores consists of a series of physical, chemical and electrochemical processes. Methods have evolved and vary with country depending on the ore source, local environmental regulations, and other factors.[1]
History

The Old Copper Complex in North America has been radiometrically dated to 9500 BP—i.e., about 7480 BCE—making it one of the oldest known examples of copper extraction in the world.[2] The earliest evidence of the cold-hammering of native copper comes from the excavation at Çayönü Tepesi in eastern Anatolia, which dates between 7200 to 6600 BCE.[3] Among the various items considered to be votive or amulets, there was one that looked like a fishhook and one like an awl. Another find, at Shanidar Cave in Mergasur, Iraq, contained copper beads, and dates back to 8,700 BCE.[4]
One of the world's oldest known copper mines, as opposed to usage of surface deposits, is at Timna Valley, Israel, and has been used since the fourth millennium BC, with surface deposit usage occurring in the fifth and sixth millennium.[5][6]
The Pločnik archaeological site in southeastern Europe (Serbia) contains the oldest securely dated evidence of copper making at high temperature, from 5,000 BCE. The find in June 2010 extends for an additional 500 years, dated to 5th millennium BCE, representing the earlier record of copper smelting from Rudna Glava (Serbia).[7]
Smelting
Until the latter half of the 20th century, smelting sulfide ores was almost the sole means of producing copper metal from mined ores (primary copper production). As of 2002, 80% of global primary copper production was from copper–iron–sulfur minerals, and the vast majority of these were treated by smelting.[8]
Copper was initially recovered from sulfide ores by directly smelting the ore in a furnace.[9] The smelters were initially located near the mines to minimize the cost of transport. This avoided the prohibitive costs of transporting the waste minerals and the sulfur and iron present in the copper-containing minerals. However, as the concentration of copper in the ore bodies decreased, the energy costs of smelting the whole ore also became prohibitive, and it became necessary to concentrate the ores first.
Initial concentration techniques included hand-sorting[10] and gravity concentration. These resulted in high losses of copper. Consequently, the development of the froth flotation process was a major step forward in mineral processing.[11] It made the development of the giant Bingham Canyon mine in Utah possible.[12]
In the twentieth century, most ores were concentrated before smelting. Smelting was initially undertaken using sinter plants and blast furnaces,[13] or with roasters and reverberatory furnaces.[14] Roasting and reverberatory furnace smelting dominated primary copper production until the 1960s.[8]
Copper smelting technology gave rise to the Copper Age, aka Chalcolithic Age, and then the Bronze Age. The Bronze Age would not have been possible without the development of smelting technology.
The modern froth flotation process was independently invented in the early 1900s in Australia by C.V Potter and around the same time by G. D. Delprat.[15]
Concentration (beneficiation)

The average grade of copper ores in the 21st century is below 0.6% copper, with a proportion of economic ore minerals being less than 2% of the total volume of the ore rock. Thus, all mining operations, the ore must usually be beneficiated (concentrated). The concentrate is typically sold to distant smelters, although some large mines have smelters located nearby. Such colocation of mines and smelters was more typical in the 19th and early 20th centuries, when smaller smelters could be economic. The subsequent processing techniques depend on the nature of the ore.
In the usual case when it is primarily sulfide copper minerals (such as chalcopyrite, FeCuS2), the ore is treated by comminution, where the rock is crushed to produce small particles (<100 μm) consisting of individual mineral phases. These particles are then ready to be separated to remove gangue (silicate rocks residues) using froth flotation.[1]
Froth flotation

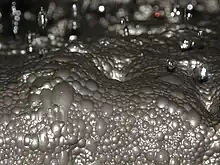
In froth flotation, the crushed ore is wetted, suspended in a slurry, and mixed with reagents that render the sulfide particles hydrophobic. Typical reagents ("collectors") include potassium ethylxanthate and sodium ethylxanthate, but dithiophosphates and dithiocarbamates are also used. The slurry is introduced to a water-filled aeration tank containing a surfactant such as methylisobutyl carbinol (MIBC). Air is constantly forced through the slurry. The air bubbles attach to the hydrophobic copper sulfide particles, which are conveyed to the surface where the froth is skimmed off. These skimmings are generally subjected to a cleaner-scavenger cell to remove excess silicates and to remove other sulfide minerals that can deleteriously impact the concentrate quality (typically, galena), and the final concentrate sent for smelting. The rock that has not floated off in the flotation cell is either discarded as tailings or further processed to extract other metals such as lead (from galena) and zinc (from sphalerite), should they exist. A variety of measures are taken to improve the efficiency of the froth flotation. Lime is used to raise the pH of the water bath, causing the collector to bond more efficiently to the copper sulfides. The process can produce a concentrates with 27–29% and 37–40% copper contents from chalcopyrite and chalcocite, respectively.
Hydrometallurgy
2.png.webp)
Oxidised copper ores include carbonates such as azurite and malachite, the silicate chrysocolla, and sulfates such as atacamite. In some cases, sulfide ores are allowed to degrade to oxides. Such ores are amenable to hydrometallurgy. Specifically, such oxide ores are usually extracted into aqueous sulfuric acid, usually in a heap leaching or dump leaching. The resulting pregnant leach solution is purified by solvent extraction (SX). It is treated with an organic solvent and an organic chelators. The chelators bind the copper ions (and no other ions, ideally), the resulting complexes dissolve in the organic phase. This organic solvent is evaporated, leaving a residue of the copper complexes. The copper ions are liberated from the residue with sulfuric acid. The barred (denuded) sulfuric acid recycled back on to the heaps. The organic ligands are recovered and recycled as well. Alternatively, the copper can be precipitated out of the pregnant solution by contacting it with scrap iron; a process called cementation. Cement copper is normally less pure than SX-EW copper.[16]
Specialized ores

Secondary sulfides—those formed by supergene secondary enrichment—are resistant (refractory) to sulfuric leaching.[17] Secondary copper sulfides are dominated by the mineral chalcocite; a mineral formed from primary sulfides, like chalcopyrite, that undergo chemical processes such as oxidation or reduction.[18] Typically, secondary sulfide ores are concentrated using froth flotation.[19] Other extraction processes like leaching are effectively used for the extraction of secondary copper sulfides, but as demand for copper rises, extraction processes tailored for low-grade ores are required, due to the depletion of copper resources.[20] Processes including in situ, dump, and heap leaching are cost-effective methods that are suitable for extracting copper from low-grade ores.[21]
Extraction processes for secondary copper sulfides and low-grade ores includes the process of heap bioleaching. Heap bioleaching presents a cost efficient extraction method that requires a less intensive energy input resulting in a higher profit.[22] This extraction process can be applied to large quantities of low-grade ores, at a lower capital cost with minimal environmental impact.[22][23]
Generally, direct froth flotation is not used to concentrate copper oxide ores, as a result of the largely ionic and hydrophilic structure of the copper oxide mineral surface.[24] Copper oxide ores are typically treated via chelating-reagent flotation and fatty-acid flotation, which use organic reagents to ensure adsorption onto the mineral surface through the formation of hydrophobic compounds on the mineral surface.[24][25]
Some supergene sulfide deposits can be leached using a bacterial oxidation heap leach process to oxidize the sulfides to sulfuric acid, which also allows for simultaneous leaching with sulfuric acid to produce a copper sulfate solution.[26][27] For oxide ores, solvent extraction and electrowinning technologies are used to recover the copper from the pregnant leach solution.[28] To ensure the best recovery of copper, it is important to acknowledge the effect copper dissolution, acid consumption, and gangue mineral composition has on the efficacy of extraction.[28]
Supergene sulfide ores rich in native copper are refractory to treatment with sulfuric acid leaching on all practicable time scales, and the dense metal particles do not react with froth flotation media. Typically, if native copper is a minor part of a supergene profile it will not be recovered and will report to the tailings. When rich enough, native copper ore bodies may be treated to recover the contained copper by gravity separation. Often, the nature of the gangue is important, as clay-rich native copper ores prove difficult to liberate. This is because clay minerals interact with flotation reagents used in extraction processes, that are then consumed, which results in minimal recovery of a high grade copper concentrate.[29]
Roasting
The roasting process is generally undertaken in combination with reverberatory furnaces. In the roaster, the copper concentrate is partially oxidised to produce "calcine". Sulfur dioxide is liberated. The stoichiometry of the reaction is:
- CuFeS2 + 3 O2 → 2 FeO + 2 CuS + 2 SO2
Roasting generally leaves more sulfur in the calcined product (15% in the case of the roaster at Mount Isa Mines[30]) than a sinter plant leaves in the sintered product (about 7% in the case of the Electrolytic Refining and Smelting smelter[31]).
As of 2005, roasting is no longer common in copper concentrate treatment because its combination with reverberatory furnaces is not energy efficient and the SO2 concentration in the roaster offgas is too dilute for cost-effective capture. Direct smelting is now favored, and uses the following smelting technologies: flash smelting, Isasmelt, Noranda, Mitsubishi or El Teniente furnaces.[8]
Smelting
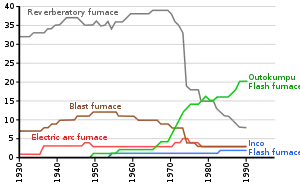

The initial melting of the material to be smelted is usually referred to as the smelting or matte smelting stage. It can be undertaken in a variety of furnaces, including the largely obsolete blast furnaces and reverberatory furnaces, as well as flash furnaces, Isasmelt furnaces, etc. The product of this smelting stage is a mixture of copper, iron and sulfur that is enriched in copper, which is called matte or copper matte.[8] The term matte grade is normally used to refer to the copper content of the matte.[32]
The purpose of the matte smelting stage is to eliminate as much of the unwanted iron, sulfur and gangue minerals (such as silica, magnesia, alumina and limestone) as possible, while minimizing the loss of copper.[8] This is achieved by reacting iron sulfides with oxygen (in air or oxygen enriched air) to produce iron oxides (mainly as FeO, but with some magnetite (Fe3O4)) and sulfur dioxide.[32]
Copper sulfide and iron oxide can mix, but when sufficient silica is added, a separate slag layer is formed.[33] Adding silica also reduces the melting point (or, more properly, the liquidus temperature) of the slag, meaning that the smelting process can be operated at a lower temperature.[33]
The slag forming reaction is:
- FeO + SiO2 → FeO.SiO2[32]
Slag is less dense than matte, so it forms a layer that floats on top of the matte.[34]
Copper can be lost from the matte in three ways: as cuprous oxide (Cu2O) dissolved in the slag,[35] as sulfide copper dissolved in the slag[36] or as tiny droplets (or prills) of matte suspended in the slag.[37][38]
The amount of copper lost as oxide copper increases as the oxygen potential of the slag increases.[38] The oxygen potential generally increases as the copper content of the matte is increased.[39] Thus, the loss of copper as oxide increases as the copper content of the matte increases.[40]
On the other hand, the solubility of sulfidic copper in slag decreases as the copper content of the matte increases beyond about 40%.[36] Nagamori calculated that more than half the copper dissolved in slags from mattes containing less than 50% copper is sulfidic copper. Above this figure, oxidic copper begins to dominate.[36]
The loss of copper as prills suspended in the slag depends on the size of the prills, the viscosity of the slag and the settling time available.[41] Rosenqvist suggested that about half the copper losses to slag were due to suspended prills.[41]
The mass of slag generated in the smelting stage depends on the iron content of the material fed into the smelting furnace and the target matte grade. The greater the iron content of the feed, the more iron that will need to be rejected to the slag for a given matte grade. Similarly, increasing the target matte grade requires the rejection of more iron and an increase in the slag volume.
Thus, the two factors that most affect the loss of copper to slag in the smelting stage are:
- matte grade
- mass of slag.[33]
This means that there is a practical limit on how high the matte grade can be if the loss of copper to slag is to be minimized. Therefore, further stages of processing (converting and fire refining) are required.
The following subsections briefly describe some of the processes used in matte smelting.
Reverberatory furnace smelting
Reverberatory furnaces are long furnaces that can treat wet, dry, or roasted concentrate. Most of the reverberatory furnaces used in the latter years treated roasted concentrate because putting dry feed materials into the reverberatory furnace is more energy efficient, and because the elimination of some of the sulfur in the roaster results in higher matte grades.[8]
The reverberatory furnace feed is added to the furnace through feed holes along the sides of the furnace, and the solid charge is melted.[8] Additional silica is normally added to help form the slag. The furnace is fired with burners using pulverized coal, fuel oil or natural gas[42]
Reverberatory furnaces can additionally be fed with molten slag from the later converting stage to recover the contained copper and other materials with a high copper content.[42]
Because the reverberatory furnace bath is quiescent, very little oxidation of the feed occurs (and thus very little sulfur is eliminated from the concentrate). It is essentially a melting process.[41] Consequently, wet-charged reverberatory furnaces have less copper in their matte product than calcine-charged furnaces, and they also have lower copper losses to slag.[42] Gill quotes a copper in slag value of 0.23% for a wet-charged reverberatory furnace vs 0.37% for a calcine-charged furnace.[42]
In the case of calcine-charged furnaces, a significant portion of the sulfur has been eliminated during the roasting stage, and the calcine consists of a mixture of copper and iron oxides and sulfides. The reverberatory furnace acts to allow these species to approach chemical equilibrium at the furnace operating temperature (approximately 1600 °C at the burner end of the furnace and about 1200 °C at the flue end;[43] the matte is about 1100 °C and the slag is about 1195 °C[42]). In this equilibration process, oxygen associated with copper compounds exchanges with sulfur associated with iron compounds, increasing the iron oxide content of the furnace, and the iron oxides interact with silica and other oxide materials to form the slag.[42]
The main equilibration reaction is:
- Cu2O + FeS → Cu2S + FeO[42]
The slag and the matte form distinct layers that can be removed from the furnace as separate streams. The slag layer is periodically allowed to flow through a hole in the wall of the furnace above the height of the matte layer. The matte is removed by draining it through a hole into ladles for it to be carried by crane to the converters.[42] This draining process is known as tapping the furnace.[42] The matte taphole is normally a hole through a water-cooled copper block that prevents erosion of the refractory bricks lining the furnace. When the removal of the matte or slag is complete, the hole is normally plugged with clay, which is removed when the furnace is ready to be tapped again.
Reverberatory furnaces were often used to treat molten converter slag to recover contained copper.[42] This would be poured into the furnaces from ladles carried by cranes. However, the converter slag is high in magnetite[44] and some of this magnetite would precipitate from the converter slag (due to its higher melting point), forming an accretion on the hearth of the reverberatory furnace and necessitating shut downs of the furnace to remove the accretion.[44] This accretion formation limits the quantity of converter slag that can be treated in a reverberatory furnace.[44]
While reverberatory furnaces have very low copper losses to slag, they are not very energy-efficient and the low concentrations of sulfur dioxide in their off-gases make its capture uneconomic. Consequently, smelter operators devoted a lot of money in the 1970s and 1980s to developing new, more efficient copper smelting processes.[45] In addition, flash smelting technologies had been developed in earlier years and began to replace reverberatory furnaces. By 2002, 20 of the 30 reverberatory furnaces still operating in 1994 had been shut down.[8]
Flash furnace smelting
In flash smelting, the concentrate is dispersed in an air or oxygen stream and the smelting reactions are largely completed while the mineral particles are still in flight.[45] The reacted particles then settle in a bath at the bottom of the furnace, where they behave like calcine in a reverberatory furnace.[46] A slag layer forms on top of the matte layer, and they can separately be tapped from the furnace.[46]
ISASMELT

The ISASMELT process is an energy-efficient smelting process that was jointly developed from the 1970s to the 1990s by Mount Isa Mines (a subsidiary of MIM Holdings and now part of Glencore) and the Government of Australia’s CSIRO. It has relatively low capital and operating costs for a smelting process.
ISASMELT technology has been applied to lead, copper, and nickel smelting. As of 2021, 22 plants were in operation in eleven countries, along with three demonstration plants located at Mt Isa. The installed capacity of copper/nickel operating plants in 2020 was 9.76 million tonnes per year of feed materials and 750 thousand tonnes per year across lead operating plants.[47]
Smelters based on the copper ISASMELT process are among the lowest-cost copper smelters in the world.[48]Converting
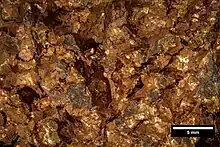
The matte, which is produced in the smelter, contains 30–70% copper (depending on the process used and the operating philosophy of the smelter), primarily as copper sulfide, as well as iron sulfide. The sulfur is removed at a high temperature as sulfur dioxide by blowing air through molten matte:
- 2 CuS + 3 O2 → 2 CuO + 2 SO2
- CuS + O2 → Cu + SO2
In a parallel reaction the iron sulfide is converted to slag:
- 2 FeS + 3 O2 → 2 FeO + 2 SO2
- 2 FeO + SiO2 → Fe2SiO4
The purity of this product is 98%, it is known as blister because of the broken surface created by the escape of sulfur dioxide gas as blister copper pigs or ingots are cooled. By-products generated in the process are sulfur dioxide and slag. The sulfur dioxide is captured and converted to sulfuric acid and either sold on the open market or used in copper leaching processes.
Refining
Fire refining
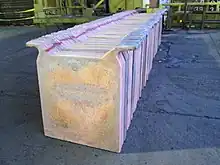
The blister copper is put into an anode furnace, a furnace that refines the blister copper to anode-grade copper in two stages by removing most of the remaining sulfur and iron, and then removing oxygen introduced during the first stage. This second stage, often referred to as poling is done by blowing natural gas, or some other reducing agent, through the molten copper oxide. When this flame burns green, indicating the copper oxidation spectrum, the oxygen has mostly been burned off. This creates copper at about 99% pure.
Electrolysis

The final stage in the production of copper is refining. Refining is achieved by electrolysis, which exploits the easy (low potential) and selective conversion of copper(II) solutions to the metal. The anodes cast from processed blister copper are placed into an aqueous solution of 3–4% copper sulfate and 10–16% sulfuric acid. Cathodes are thin rolled sheets of highly pure copper or, more commonly these days, reusable stainless steel starting sheets (as in the IsaKidd process).[49] A potential of only 0.2–0.4 volts is required for the process to commence. In industrial plants current densities up to 420 A/m2 are possible.[50]
At the anode (oxidation reaction), copper and less noble metals dissolve. More noble metals and less soluble elements such as silver, gold, selenium, and tellurium settle to the bottom of the cell as anode slime, which forms a salable by-product. Copper(II) ions migrate through the electrolyte to the cathode. At the cathode (reduction reaction), Cu2+ ions are reduced in copper metal and Cu(s) plates out, but less noble constituents such as arsenic and zinc remain in solution unless a higher voltage is used.[51]
The reactions involving metallic copper and Cu2+ ions at the electrodes are the following:
Concentrate and copper marketing
Copper concentrates produced by mines are sold to smelters and refiners who treat the ore and refine the copper and charge for this service via treatment charges (TCs) and refining charges (RCs). The TCs are charged in US$ per tonne of concentrate treated and RCs are charged in cents per pound treated, denominated in US dollars, with benchmark prices set annually by major Japanese smelters. The customer in this case can be a smelter, who on-sells blister copper ingots to a refiner, or a smelter-refiner which is vertically integrated.
One prevalent form of copper concentrate contains gold and silver, like the one produced by Bougainville Copper Limited from the Panguna mine from the early 1970s to the late 1980s.[52]
The typical contract for a miner is denominated against the London Metal Exchange price, minus the TC-RCs and any applicable penalties or credits. Penalties may be assessed against copper concentrates according to the level of deleterious elements such as arsenic, bismuth, lead or tungsten. Because a large portion of copper sulfide ore bodies contain silver or gold in appreciable amounts, a credit can be paid to the miner for these metals if their concentration within the concentrate is above a certain amount. Usually the refiner or smelter charges the miner a fee based on the concentration; a typical contract will specify that a credit is due for every ounce of the metal in the concentrate above a certain concentration; below that, if it is recovered, the smelter will keep the metal and sell it to defray costs.
Copper concentrate is traded either via spot contracts or under long term contracts as an intermediate product in its own right. Often the smelter sells the copper metal itself on behalf of the miner. The miner is paid the price at the time that the smelter-refiner makes the sale, not at the price on the date of delivery of the concentrate. Under a Quotational Pricing system, the price is agreed to be at a fixed date in the future, typically 90 days from time of delivery to the smelter.
A-grade copper cathode is of 99.99% copper in sheets that are 1 cm thick, and approximately 1 meter square weighing approximately 200 pounds. It is a true commodity, deliverable to and tradeable upon the metal exchanges in New York City (COMEX), London (London Metals Exchange) and Shanghai (Shanghai Futures Exchange). Often copper cathode is traded upon the exchanges indirectly via warrants, options, or swap contracts such that the majority of copper is traded upon the LME/COMEX/SFE, but delivery is achieved directly, logistically moving the physical copper, and transferring the copper sheet from the physical warehouses themselves.
The chemical specification for electrolytic grade copper is ASTM B 115-00 (a standard that specifies the purity and maximum electrical resistivity of the product).
Peak copper

Peak copper is the point in time at which the maximum global copper production rate is reached. Since copper is a finite resource, at some point in the future new production from mining will diminish, and at some earlier time production will reach a maximum. When this will occur is a matter of dispute. Unlike fossil fuels, copper is scrapped and reused, and it has been estimated that at least 80% of all copper ever mined is still available (having been repeatedly recycled).[53]
Copper is among the most important industrial metals, ranking third after iron and aluminium in terms of quantity used.[54] It is valued for its heat and electrical conductivities, ductility, malleability and resistance to corrosion. Electrical uses account for about three quarters of total copper consumption, including power cables, data cables and electrical equipment. It is also used in cooling and refrigeration tubing, heat exchangers, water pipes and consumer products.[54]
Copper has been used by humans for at least 10,000 years. More than 97% of all copper ever mined and smelted has been extracted since 1900. The increased demand for copper due to the growing Indian and Chinese economies since 2006 has led to increased prices and an increase in copper theft.[55]
History
Concern about the copper supply is not new. In 1924 geologist and copper-mining expert Ira Joralemon warned:[56]
- ... the age of electricity and of copper will be short. At the intense rate of production that must come, the copper supply of the world will last hardly a score of years. ... Our civilization based on electrical power will dwindle and die.
Copper supply
.svg.png.webp)
Globally, economic copper resources are being depleted with the equivalent production of three world-class copper mines being consumed annually.[55] Environmental analyst Lester Brown suggested in 2008 that copper might run out within 25 years based on what he considered a reasonable extrapolation of 2% growth per year.[57]
New copper discoveries
Fifty-six new copper discoveries have been made during the three decades 1975–2005.[55] World discoveries of new copper deposits are said to have peaked in 1996.[58] However, according to the US Geological Survey (USGS), remaining world copper reserves have more than doubled since then, from 310 million metric tons in 1996[59] to 890 million metric tons in 2022.[60]
Production

As shown in the table below, the three chief national producers of copper, respectively, in 2002, were Chile, Indonesia, and the United States. In 2013, they were Chile, China, and Peru. Twenty-one of the 28 largest copper mines in the world (as of 2006) are not amenable to expansion.[55]
Country | 2002 | 2003 | 2004 | 2005 | 2006 | 2007 | 2008 | 2009 | 2010 | 2011 | 2012 | 2013 | 2014 | 2015 |
---|---|---|---|---|---|---|---|---|---|---|---|---|---|---|
![]() |
4,580 | 4,860 | 5,410 | 5,320 | 5,560 | 5,700 | 5,330 | 5,390 | 5,420 | 5,260 | 5,430 | 5,780 | 5,750 | 5,760 |
![]() |
585 | 565 | 620 | 640 | 890 | 920 | 950 | 995 | 1,190 | 1,310 | 1,630 | 1,600 | 1,760 | 1,710 |
![]() |
843 | 850 | 1,040 | 1,090 | 1,049 | 1,200 | 1,270 | 1,275 | 1,250 | 1,240 | 1,300 | 1,380 | 1,380 | 1,700 |
![]() |
1,140 | 1,120 | 1,160 | 1,150 | 1,200 | 1,190 | 1,310 | 1,180 | 1,110 | 1,110 | 1,170 | 1,250 | 1,360 | 1,380 |
![]() |
873 | 870 | 854 | 930 | 859 | 860 | 886 | 854 | 870 | 958 | 958 | 990 | 970 | 971 |
![]() |
N/A | N/A | N/A | N/A | N/A | N/A | N/A | N/A | 343 | 520 | 600 | 970 | 1,030 | 1,020 |
![]() |
695 | 700 | 675 | 675 | 725 | 730 | 750 | 725 | 703 | 713 | 883 | 833 | 742 | 732 |
![]() |
330 | 330 | 427 | 450 | 476 | 530 | 546 | 697 | 690 | 668 | 690 | 760 | 708 | 712 |
![]() |
600 | 580 | 546 | 580 | 607 | 585 | 607 | 491 | 525 | 566 | 579 | 632 | 696 | 697 |
![]() |
1,160 | 1,170 | 840 | 1,050 | 816 | 780 | 651 | 996 | 872 | 543 | 360 | 504 | N/A | N/A |
![]() |
330 | 330 | 406 | 420 | 338 | 400 | 247 | 238 | 260 | 443 | 440 | 480 | 515 | 594 |
![]() |
490 | 480 | 461 | 400 | 457 | 460 | 420 | 390 | 380 | 417 | 424 | 446 | N/A | N/A |
![]() |
503 | 500 | 531 | 530 | 512 | 470 | 430 | 439 | 425 | 427 | 427 | 429 | N/A | N/A |
Other countries | 1,500 | 1,500 | 1,610 | 1,750 | 1,835 | 1,800 | 2,030 | 2,190 | 1,900 | 1,970 | 2,000 | 2,200 | 3,600 | 3,800 |
World | 13,600 | 13,800 | 14,700 | 15,000 | 15,100 | 15,500 | 15,600 | 16,100 | 16,100 | 16,100 | 16,900 | 18,200 | 18,400 | 19,100 |
Reserves
Copper is a fairly common element, with an estimated concentration of 50–70 ppm (0.005–0.007 percent) in Earth's crust (1 kg of copper per 15–20 tons of crustal rock).[73] A concentration of 60 ppm would multiply out to 1.66 quadrillion tonnes over the 2.77×1022 kg mass of the crust,[74] or over 90 million years' worth at the 2013 production rate of 18.3 MT per year. However, not all of it can be extracted profitably at the current level of technology and the current market value.
The USGS reported a current total reserve base of copper in potentially recoverable ores of 1.6 billion tonnes as of 2005, of which 950 million tonnes were considered economically recoverable.[75] A 2013 global assessment identified "455 known deposits (with well-defined identified resources) that contain about 1.8 billion metric tons of copper", and predicted "a mean of 812 undiscovered deposits within the uppermost kilometer of the earth's surface" containing another 3.1 billion metric tons of copper "which represents about 180 times 2012 global copper production from all types of copper deposits."[76]
Country | 1996 Reserves | Percent | 2015 Reserves | Percent |
---|---|---|---|---|
![]() |
88,000 | 28.4% | 209,000 | 29.9% |
![]() |
7,000 | 2.26% | 93,000 | 13.2% |
![]() |
7,000 | 2.26% | 68,000 | 9.71% |
![]() |
N/A | N/A | 38,000 | 5.43% |
![]() |
45,000 | 14.5% | 35,000 | 5.00% |
![]() |
3,000 | 0.968% | 30,000 | 4.29% |
![]() |
20,000 | 6.45% | 30,000 | 4.29% |
![]() |
20,000 | 6.45% | 28,000 | 4.00% |
![]() |
11,000 | 3.55% | 25,000 | 3.57% |
![]() |
N/A | N/A | 20,000 | 2.86% |
![]() |
12,000 | 3.87% | 20,000 | 2.86% |
![]() |
11,000 | 3.55% | 11,000 | 1.57% |
![]() |
14,000 | 4.52% | 6,000 | 0.86% |
![]() |
11,000 | 3.55% | N/A | N/A |
![]() |
7,000 | 2.26% | N/A | N/A |
Other countries | 55,000 | 17.7% | 90,000 | 12.9% |
World | 310,000 | 100% | 700,000 | 100% |
Known resources
Recycling
In the US, more copper is recovered and put back into service from recycled material than is derived from newly mined ore. Copper's recycle value is so great that premium-grade scrap normally has at least 95% of the value of primary metal from newly mined ore.[78] In Europe, about 50% of copper demand comes from recycling (as of 2016).[79]
As of 2011, recycled copper provided 35% of total worldwide copper usage.[80]
Undiscovered conventional resources
Based on discovery rates and existing geologic surveys, researchers estimated in 2006 that 1.6 billion metric tons of copper could be brought into use. This figure relied on the broadest possible definition of available copper as well as a lack of energy constraints and environmental concerns.[75]
The US Geological Survey estimated that, as of 2013, there remained 3.5 billion metric tons of undiscovered copper resources worldwide in porphyry and sediment-hosted type deposits, two types which currently provide 80% of mined copper production. This was in addition to 2.1 billion metric tons of identified resources. Combined identified and estimated undiscovered copper resources were 5.6 billion metric tons,[81] 306 times the 2013 global production of newly mined copper of 18.3 million metric tons.
Unconventional resources
Deep-sea nodules are estimated to contain 700 million tonnes of copper.[63]
Criticism
Julian Simon was a senior fellow at the Cato Institute and a professor of business and economics. In his book The Ultimate Resource 2 (first printed in 1981 and reprinted in 1998), he extensively criticizes the notion of "peak resources", and uses copper as one example. He argues that, even though "peak copper" has been a persistent scare since the early 20th century, "known reserves" grew at a rate that outpaced demand, and the price of copper was not rising but falling over the long run. For example, even though world production of copper in 1950 was only one-eighth of what it was in the early 2000s, known reserves were also much lower at the time – around 100 million metric tons – making it appear that the world would run out of copper in 40 to 50 years at most.
Simon's own explanation for this development is that the very notion of known reserves is deeply flawed,[82] as it does not take into account changes in mining profitability. As richer mines are exhausted, developers turn their attention to poorer sources of the element and eventually develop cheap methods of extracting it, raising known reserves. Thus, for example, copper was so abundant 5000 years ago, occurring in pure form as well as in highly concentrated copper ores, that prehistoric peoples were able to collect and process it with very basic technology. As of the early 21st century, copper is commonly mined from ores that contain 0.3–0.6% copper by weight. Yet, despite the material being far less widespread, the cost of, for example, a copper pot was vastly lower in the late 20th century than 5000 years ago.[83]
See also
References
- 1 2 Lossin, Adalbert (2001). "Copper". Ullmann's Encyclopedia of Industrial Chemistry. doi:10.1002/14356007.a07_471. ISBN 3527306730.
- ↑ Malakof, David (19 March 2021). "Ancient Native Americans were among the world's first coppersmiths". Science. Retrieved 6 June 2022.
- ↑ Braidwood, Robert J.; Çambel, Halet; Redman, Charles L.; Watson, Patty Jo (1971). "Beginnings of Village-Farming Communities in Southeastern Turkey". Proc Natl Acad Sci U S A. 68 (6): 1236–1240. Bibcode:1971PNAS...68.1236B. doi:10.1073/pnas.68.6.1236. PMC 389161. PMID 16591930.
- ↑ R.S. Solecki; R.L. Solecki; A.P. Agelarakis (2004). The Proto-neolithic Cemetery in Shanidar Cave. Texas A&M University Press. p. 53. ISBN 978-1585442720.
- ↑ Shaw, Ian (2002). A Dictionary of Archaeology. John Wiley & Sons. pp. 582–583. ISBN 978-0631235835.
- ↑ King, PJ; Stager, LE (2001). Life In Biblical Israel. Westminster John Knox Press. p. 165. ISBN 978-0664221485.
timna millennium.
- ↑ "Serbian site may have hosted first copper makers". ScienceNews. July 17, 2010. Archived from the original on May 8, 2013. Retrieved January 3, 2013.
- 1 2 3 4 5 6 7 8 W G Davenport, M King, M Schlesinger and A K Biswas, Extractive Metallurgy of Copper, Fourth Edition (Elsevier Science Limited: Kidlington, Oxford, England, 2002).
- ↑ Robert Raymond, Out of the Fiery Furnace, The MacMillan Company of Australia Pty Ltd, Melbourne, 1984.
- ↑ C B Gill, Non-ferrous Extractive Metallurgy (John Wiley & Sons, New York, 1980) p. 32
- ↑ Robert Raymond (1984) Out of the Fiery Furnace, The MacMillan Company of Australia Pty Ltd, Melbourne, pp. 233–235, ISBN 027100441X.
- ↑ "BP Minerals completes US$400 million modernization at Bingham Canyon," Mining Engineering, November 1988, 1017–1020.
- ↑ S A Bradford (1989) "The historical development of copper smelting in British Columbia," in: All that Glitters: Readings in Historical Metallurgy, Ed. Michael L. Wayman, The Canadian Institute of Mining and Metallurgy: Montreal, pp. 162–165, ISBN 0919086241.
- ↑ E Kossatz and P J Mackey (1989) "The first copper smelter in Canada," in: All that Glitters: Readings in Historical Metallurgy, Ed. Michael L. Wayman, The Canadian Institute of Mining and Metallurgy: Montreal, pp. 160–161, ISBN 0919086241.
- ↑ "Historical Note". Minerals Separation Ltd. Retrieved 2007-12-30.
- ↑ Tasker, Peter A.; Tong, Christine C.; Westra, Arjan N. (2007). "Co-extraction of Cations and Anions in Base Metal Recovery". Coordination Chemistry Reviews. 251 (13–14): 1868–1877. doi:10.1016/j.ccr.2007.03.014.
- ↑ Petersen, Jochen (October 2016). "Heap leaching as a key technology for recovery of values from low-grade ores – A brief overview". Hydrometallurgy. 165: 206–212. doi:10.1016/j.hydromet.2015.09.001.
- ↑ Wu, Biao; Yang, Xinlong; Wen, Jiankang; Wang, Dianzuo (2019-11-05). "Semiconductor-Microbial Mechanism of Selective Dissolution of Chalcocite in Bioleaching". ACS Omega. 4 (19): 18279–18288. doi:10.1021/acsomega.9b02294. ISSN 2470-1343. PMC 6844112. PMID 31720528.
- ↑ Rahman, Reza M.; Ata, Seher; Jameson, Graeme J. (November 2013). "Froth recovery measurements in an industrial flotation cell". Minerals Engineering. 53: 193–202. doi:10.1016/j.mineng.2013.08.003. ISSN 0892-6875.
- ↑ Yu, Shichao; Liao, Rui; Yang, Baojun; Fang, Chaojun; Wang, Zhentang; Liu, Yuling; Wu, Baiqiang; Wang, Jun; Qiu, Guanzhou (January 2022). "Chalcocite (bio)hydrometallurgy—current state, mechanism, and future directions: A review". Chinese Journal of Chemical Engineering. 41: 109–120. doi:10.1016/j.cjche.2021.12.014. ISSN 1004-9541. S2CID 245562646.
- ↑ Watling, H. R. (October 2006). "The bioleaching of sulphide minerals with emphasis on copper sulphides — A review". Hydrometallurgy. 84 (1): 81–108. doi:10.1016/j.hydromet.2006.05.001. ISSN 0304-386X.
- 1 2 Panda, Sandeep; Akcil, Ata; Pradhan, Nilotpala; Deveci, Haci (November 2015). "Current scenario of chalcopyrite bioleaching: A review on the recent advances to its heap-leach technology". Bioresource Technology. 196: 694–706. doi:10.1016/j.biortech.2015.08.064. ISSN 0960-8524. PMID 26318845. S2CID 2254790.
- ↑ Brierley, C. L. (December 2008). "How will biomining be applied in future?". Transactions of Nonferrous Metals Society of China. 18 (6): 1302–1310. doi:10.1016/S1003-6326(09)60002-9. ISSN 1003-6326.
- 1 2 Feng, Qicheng; Yang, Wenhang; Wen, Shuming; Wang, Han; Zhao, Wenjuan; Han, Guang (November 2022). "Flotation of copper oxide minerals: A review". International Journal of Mining Science and Technology. 32 (6): 1351–1364. doi:10.1016/j.ijmst.2022.09.011. ISSN 2095-2686. S2CID 253788625.
- ↑ Fuerstenau, D. W.; Herrera-Urbina, R.; McGlashan, D. W. (February 2000). "Studies on the applicability of chelating agents as universal collectors for copper minerals". International Journal of Mineral Processing. 58 (1): 15–33. doi:10.1016/S0301-7516(99)00058-7. ISSN 0301-7516.
- ↑ Kariuki, Stephen; Moore, Cory; McDonald, Andrew M. (March 2009). "Chlorate-based oxidative hydrometallurgical extraction of copper and zinc from copper concentrate sulfide ores using mild acidic conditions". Hydrometallurgy. 96 (1): 72–76. doi:10.1016/j.hydromet.2008.08.008. ISSN 0304-386X.
- ↑ Robertson, S.W.; Van Staden, P.J.; Seyedbagheri, A. (December 2012). "Advances in high-temperature heap leaching of refractory copper sulphide ores" (PDF). Journal of the Southern African Institute of Mining and Metallurgy. 112 (12): 1045–1050 – via ResearchGate.
- 1 2 Ochromowicz, Katarzyna; Chmielewski, Tomasz (January 2008). "Growing Role of Solvent Extraction in Copper Ores Processing". Fizykochemiczne Problemy Mineralurgii. 42: 29–36.
- ↑ Han, Baisui; Altansukh, Batnasan; Haga, Kazutoshi; Stevanović, Zoran; Jonović, Radojka; Avramović, Ljiljana; Urosević, Daniela; Takasaki, Yasushi; Masuda, Nobuyuki; Ishiyama, Daizo; Shibayama, Atsushi (2018-06-15). "Development of copper recovery process from flotation tailings by a combined method of high‒pressure leaching‒solvent extraction". Journal of Hazardous Materials. 352: 192–203. doi:10.1016/j.jhazmat.2018.03.014. ISSN 0304-3894. PMID 29609151. S2CID 4879400.
- ↑ B V Borgelt, G E Casley and J Pritchard (1974) "Fluid Bed Roasting at Mount Isa," The Aus. I.M.M. North West Queensland Branch, Regional Meeting, August 1974. The Australasian Institute of Mining and Metallurgy: Melbourne, pp. 123–130.
- ↑ P J Wand (1980) "Copper smelting at Electrolytic Refining and Smelting Company of Australia Ltd., Port Kembla, N.S.W.", in: Mining and Metallurgical Practices in Australasia: The Sir Maurice Mawby Memorial Volume, Ed J T Woodcock. The Australasian Institute of Mining and Metallurgy: Melbourne. pp. 335–340.
- 1 2 3 W G Davenport, M King, M Schlesinger and A K Biswas, Extractive Metallurgy of Copper, Fourth Edition (Elsevier Science Limited: Kidlington, Oxford, England, 2002), pp. 57–72.
- 1 2 3 P C Hayes, Process Principles in Minerals and Materials Production (Hayes Publishing Company: Brisbane, 1993), pp. 173–179.
- ↑ C B Gill, Non-ferrous Extractive Metallurgy (John Wiley & Sons, New York, 1980) p. 19
- ↑ R Altman and H H Kellogg, "Solubility of copper in silica-saturated iron silicate slag," Transactions of the Institution of Mining and Metallurgy (Section C: Mineral Processing and Extractive Metallurgy), 81, September 1972, C163–C175.
- 1 2 3 M. Nagamori (1974). "Metal loss to slag: Part I. Sulfidic and oxidic dissolution of copper in fayalite slag from low grade matte". Metallurgical Transactions. 5 (3): 531–538. Bibcode:1974MT......5..531N. doi:10.1007/BF02644646. S2CID 135507603.
- ↑ A Yazawa and S Nakazawa, "Evaluation of non-equilibrium minor components in pyrometallurgy," in: EPD Congress 1998, Ed. B Mishra (The Minerals, Metals and Materials Society: Warrendale, Pennsylvania, 1998), pp. 641–655.
- 1 2 B J Elliott, J B See, and W J Rankin, "Effect of slag composition on copper losses to silica-saturated iron silicate slags," Transactions of the Institution of Mining and Metallurgy (Section C: Mineral Processing and Extractive Metallurgy), September 1978, C–C211.
- ↑ Matousek, J (1993). "Oxygen potentials of copper smelting slags". Canadian Metallurgical Quarterly. 32 (2): 97–101. Bibcode:1993CaMQ...32...97M. doi:10.1179/cmq.1993.32.2.97.
- ↑ P J Mackey (2011). "The Physical Chemistry of Copper Smelting Slags and Copper Losses at the Paipote SmelterPart 2 – Characterisation of industrial slags". Canadian Metallurgical Quarterly. 50 (4): 330–340. Bibcode:2011CaMQ...50..330C. doi:10.1179/000844311X13112418194806. S2CID 137350753.
- 1 2 3 T Rosenqvist (2004) Principles of Extractive Metallurgy, Second Edition, Tapir Academic Press: Trondheim, p. 331, ISBN 8251919223.
- 1 2 3 4 5 6 7 8 9 10 C B Gill, Non-ferrous Extractive Metallurgy (John Wiley & Sons, New York, 1980) pp. 29–35
- ↑ C B Gill, Non-ferrous Extractive Metallurgy (John Wiley & Sons, New York, 1980) p. 23
- 1 2 3 G E Casley, J Middlin and D White, "Recent developments in reverberatory furnace and converter practice at the Mount Isa Mines copper smelter," in: Extractive Metallurgy of Copper, Volume 1, (The Metallurgical Society: Warrendale, Pennsylvania, 1976), pp. 117–138.
- 1 2 P J Mackey and P Tarassoff, "New and emerging technologies in sulphide [sic] smelting," in: Advances in Sulfide Smelting Volume 2: Technology and Practice, Eds H Y Sohn, D B George and A D Zunkel (The Metallurgical Society of the American Institute of Mining, Metallurgical and Petroleum Engineers: Warrendale, Pennsylvania, 1983), pp. 399–426.
- 1 2 W G Davenport, M King, M Schlesinger and A K Biswas, Extractive Metallurgy of Copper, Fourth Edition (Elsevier Science Limited: Kidlington, Oxford, England, 2002), pp. 73–102.
- ↑ "ISASMELT Technology Brochure" (PDF). Retrieved 26 September 2021.
- ↑ J L Bill, T E Briffa, A S Burrows, C R Fountain, D Retallick, J M I Tuppurainen, J S Edwards, and P Partington, "Isasmelt—Mount Isa copper smelter progress update," in: Sulfide Smelting 2002, Eds R L Stephens and H Y Sohn (The Minerals, Metals and Materials Society: Warrendale, Pennsylvania), 2002, 181–193.
- ↑ Robinson T. (2002). "Electrolytic refining." pp. 265–288 in: Extractive Metallurgy of Copper, Fourth Edition. Eds Davenport W. G., King M., Schlesinger M., and Biswas A. K. (Elsevier Science Limited: Kidlington, Oxford, England).
- ↑ Filzwieser A, Hanel MB, Filzwieser I, Wallner S (May 13, 2019). FAQS with regard to operating a Cu ER tankhouse above 400 A/m2 (PDF) (Report).
- ↑ Samans, Carl H. (1949). Engineering Metals and their Alloys. MacMillan.
- ↑ "About the Company". Archived from the original on 23 September 2015. Retrieved 24 August 2015.
- ↑ "Copper Recycling". Copper Alliance. 2021. Retrieved 2023-02-08.
- 1 2 National Minerals Information Center. "Copper Statistics and Information". United States Geological Survey. Retrieved 2023-02-08.
- 1 2 3 4 Leonard, Andrew (2 March 2006). "Peak copper?". Salon. Retrieved 23 March 2008.
- ↑ "Copper and electricity to vanish in twenty years?". Engineering and Mining Journal. 118 (4): 122. 26 July 1924.
- ↑ Brown, Lester (2006). Plan B 2.0: Rescuing a Planet Under Stress and a Civilization in Trouble. New York: W.W. Norton. p. 109. ISBN 0-393-32831-7.
- ↑ "Peak Copper Means Peak Silver". Charleston Voice. 29 December 2005. Archived from the original on 4 November 2013. Retrieved 9 April 2008.
- ↑ Edelstein, Daniel L. (February 1997). "Copper" (PDF). Mineral Commodity Surveys. U.S. Geological Survey. p. 53. Retrieved 2023-02-08.
- ↑ Flanagan, Daniel M. (January 2023). "Copper" (PDF). Mineral Commodity Surveys. U.S. Geological Survey. p. 2. Retrieved 2023-02-08.
- ↑ "pg. 54 – Copper" (PDF). USGS. 2004. Retrieved 9 April 2008.
- ↑ "pg. 56 – Copper" (PDF). USGS. 2006. Retrieved 9 April 2008.
- 1 2 "pg. 54 – Copper" (PDF). USGS. 2008. Retrieved 9 April 2008.
- ↑ "pg. 49 – Copper" (PDF). USGS. 2010. Retrieved 15 July 2012.
- ↑ "pg. 49 – Copper" (PDF). USGS. 2011. Retrieved 29 March 2015.
- ↑ "pg. 49 – Copper" (PDF). USGS. 2012. Retrieved 15 July 2012.
- ↑ "pg. 49 – Copper" (PDF). USGS. 2013. Retrieved 29 March 2015.
- ↑ "pg. 48 – Copper" (PDF). USGS. 2014. Retrieved 11 April 2014.
- 1 2 "pg. 49 – Copper" (PDF). USGS. 2015. Retrieved 29 March 2015.
- ↑ "pg. 55 – Copper" (PDF). USGS. 2016. Retrieved 29 March 2017.
- ↑ "pg. 55 – Copper" (PDF). USGS. 2017. Retrieved 29 March 2017.
- ↑ "Copper Statistics". USGS. 2016. Retrieved 29 March 2017.
- ↑ Emsley, John (2003). Nature's building blocks: an A–Z guide to the elements. Oxford University Press. pp. 121–125. ISBN 978-0-19-850340-8.
- ↑ Peterson, B. T.; Depaolo, D. J. (December 2007). Mass and Composition of the Continental Crust Estimated Using the CRUST2.0 Model. American Geophysical Union Fall Meeting Abstracts. Bibcode:2007AGUFM.V33A1161P. V33A–1161.
- 1 2 Biello, David (17 January 2006). "Measure of Metal Supply Finds Future Shortage". Scientific American. Retrieved 23 March 2008.
- ↑ Hammarstrom, Jane M. (29 October 2013). "Undiscovered Porphyry Copper Resources—A Global Assessment". The Geological Society of America: Annual Meeting & Expo. Retrieved 12 April 2014.
- ↑ "pg. 50 – Copper" (PDF). USGS. 1996. Retrieved 12 April 2014.
- ↑ "Copper in the USA: Bright Future – Glorious Past". Copper Development Association. Archived from the original on 15 August 2013. Retrieved 9 April 2008.
- ↑ "Europe's Copper Industry". Archived from the original on 10 August 2020. Retrieved 10 January 2019.
- ↑ International Copper Study Group, The World Copper Factbook 2012, p. 50, archived from the original on 5 January 2013, retrieved 2023-02-08
{{citation}}
: CS1 maint: bot: original URL status unknown (link) - ↑ Kathleen M. Johnson and others, Estimate of undiscovered copper resources of the world, 2013, US Geological Survey, Fact Sheet 2014–3004, Jan. 2014.
- ↑ Simon, Julian (16 February 1998) Chapt 12, "People, Materials, and Environment" in The Ultimate Resource II.
- ↑ Simon, Julian (1998). "The Ultimate Resource II: People, Materials, and Environment". Retrieved 2023-02-08.
External links
- Copper.org
- "US Minerals Databrowser". Mazama Science. Archived from the original on 11 March 2011. Retrieved 25 March 2010.
- R. B. Gordon*, M. Bertram and T. E. Graedel (31 January 2006). "Metal Stocks and Sustainability". Proceedings of the National Academy of Sciences. U.S. National Academy of Sciences. 103 (5): 1209–1214. Bibcode:2006PNAS..103.1209G. doi:10.1073/pnas.0509498103. PMC 1360560. PMID 16432205.
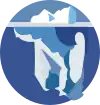
- The Copper Development Association's copper production Archived 2013-09-07 at the Wayback Machine page.
- Copper Processing, from an online text on metals, Illinois Sustainable Technology Center, University of Illinois, archived in May 2017
- National Pollutant Inventory – Copper and copper compounds fact sheet
- University of Pittsburgh School of Engineering Chemical and Petroleum Engineering Department, Froth Flotation Archived 2005-12-06 at the Wayback Machine Lab notes.
- Copper Mine, college course syllabus, emphasis on chemistry, last updated 2000
Bibliography
- Gill, C. B. (1980) Nonferrous Extractive Metallurgy, John Wiley and Sons: New York, ISBN 0471059803