Hydrogen gas is produced by several industrial methods. Fossil fuels are the dominant source of hydrogen.[1] As of 2020, the majority of hydrogen (~95%) is produced by steam reforming of natural gas and other light hydrocarbons, and partial oxidation of heavier hydrocarbons.[2] Other methods of hydrogen production include biomass gasification and methane pyrolysis. Methane pyrolysis and water electrolysis can use any source of electricity including renewable energy.
The production of hydrogen plays a key role in any industrialized society, since hydrogen is required for many chemical processes.[3] In 2020, roughly 87 million tons of hydrogen was produced[4] worldwide for various uses, such as oil refining, in the production of ammonia through the Haber process, and in the production of methanol through reduction of carbon monoxide. The global hydrogen generation market was fairly valued at US$155 billion in 2022, and expected to grow at a compound annual growth rate of 9.3% from 2023 to 2030.[5]
Steam methane reforming
Steam methane reforming (SMR) produces hydrogen from natural gas, mostly methane (CH4), and water. It is the cheapest source of industrial hydrogen, being the source of nearly 50% of the world's hydrogen.[6] The process consists of heating the gas to 700–1,100 °C (1,300–2,000 °F) in the presence of steam over a nickel catalyst. The resulting endothermic reaction forms carbon monoxide and molecular hydrogen (H2).[7]
In the water-gas shift reaction, the carbon monoxide reacts with steam to obtain further quantities of H2. The WGSR also requires a catalyst, typically over iron oxide or other oxides. The byproduct is CO2.[7] Depending on the quality of the feedstock (natural gas, naphtha, etc.), one ton of hydrogen produced will also produce 9 to 12 tons of CO2, a greenhouse gas that may be captured.[8]

For this process, high temperature steam (H2O) reacts with methane (CH4) in an endothermic reaction to yield syngas.[9]
- CH4 + H2O → CO + 3 H2
In a second stage, additional hydrogen is generated through the lower-temperature, exothermic, water-gas shift reaction, performed at about 360 °C (680 °F):
- CO + H2O → CO2 + H2
Essentially, the oxygen (O) atom is stripped from the additional water (steam) to oxidize CO to CO2. This oxidation also provides energy to maintain the reaction. Additional heat required to drive the process is generally supplied by burning some portion of the methane.
Other fossil fuel methods
Partial oxidation
Hydrogen production from natural gas and heavier hydrocarbons is achieved by partial oxidation. A fuel-air or fuel-oxygen mixture is partially combusted, resulting in a hydrogen- and carbon monoxide-rich syngas. More hydrogen and carbon dioxide are then obtained from carbon monoxide (and water) via the water-gas shift reaction.[7] Carbon dioxide can be co-fed to lower the hydrogen to carbon monoxide ratio.
The partial oxidation reaction occurs when a substoichiometric fuel-air mixture or fuel-oxygen is partially combusted in a reformer or partial oxidation reactor. A distinction is made between thermal partial oxidation (TPOX) and catalytic partial oxidation (CPOX). The chemical reaction takes the general form:
- 2 CnHm + nO2 → 2n CO + mH2
Idealized examples for heating oil and coal, assuming compositions C12H24 and C24H12 respectively, are as follows:
- C12H24 + 6 O2 → 12 CO + 12 H2
- C24H12 + 12 O2 → 24 CO + 6 H2
Plasma reforming
The Kværner process or Kvaerner carbon black & hydrogen process (CB&H)[10] is a plasma reforming method, developed in the 1980s by a Norwegian company of the same name, for the production of hydrogen and carbon black from liquid hydrocarbons (CnHm). Of the available energy of the feed, approximately 48% is contained in the hydrogen, 40% is contained in activated carbon and 10% in superheated steam.[11] CO2 is not produced in the process.
A variation of this process is presented in 2009 using, plasma arc waste disposal technology for the production of hydrogen, heat and carbon from methane and natural gas in a plasma converter.[12]
Coal
For the production of hydrogen from coal, coal gasification is used. The process of coal gasification uses steam and oxygen to break molecular bonds in coal and form a gaseous mixture of hydrogen and carbon monoxide.[13] Carbon dioxide and pollutants may be more easily removed from gas obtained from coal gasification versus coal combustion.[14][15] Another method for conversion is low-temperature and high-temperature coal carbonization.[16]
Coke oven gas made from pyrolysis (oxygen free heating) of coal has about 60% hydrogen, the rest being methane, carbon monoxide, carbon dioxide, ammonia, molecular nitrogen, and hydrogen sulfide (H2S). Hydrogen can be separated from other impurities by the pressure swing adsorption process. Japanese steel companies have carried out production of hydrogen by this method.
Petroleum coke
Petroleum coke can also be converted to hydrogen-rich syngas via coal gasification. The produced syngas consists mainly of hydrogen, carbon monoxide and H2S from the sulfur in the coke feed. Gasification is an option for producing hydrogen from almost any carbon source.[17]
Depleted oil wells
Injecting appropriate microbes into depleted oil wells allows them to extract hydrogen from the remaining, unrecoverable oil. Since the only inputs are the microbes, production costs are low. The method also produces concentrated CO
2 that could in principle be captured.[18]
From water
Methods to produce hydrogen without the use of fossil fuels involve the process of water splitting, or splitting the water molecule (H2O) into its components oxygen and hydrogen. When the source of energy for water splitting is renewable or low-carbon, the hydrogen produced is sometimes referred to as green hydrogen. The conversion can be accomplished in several ways, but all methods are currently considered more expensive than fossil-fuel based production methods.
Electrolysis of water
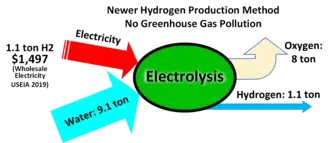
Water electrolysis is using electricity to split water into hydrogen and oxygen. As of 2020, less than 0.1% of hydrogen production comes from water electrolysis.[19] Electrolysis of water is 70–80% efficient (a 20–30% conversion loss)[20][21] while steam reforming of natural gas has a thermal efficiency between 70 and 85%.[22] The electrical efficiency of electrolysis is expected to reach 82–86%[23] before 2030, while also maintaining durability as progress in this area continues apace.[24]
Water electrolysis can operate at 50–80 °C (120–180 °F), while steam methane reforming requires temperatures at 700–1,100 °C (1,300–2,000 °F).[25] The difference between the two methods is the primary energy used; either electricity (for electrolysis) or natural gas (for steam methane reforming). Due to their use of water, a readily available resource, electrolysis and similar water-splitting methods have attracted the interest of the scientific community. With the objective of reducing the cost of hydrogen production, renewable sources of energy have been targeted to allow electrolysis.[13]
There are three main types of electrolytic cells, solid oxide electrolyser cells (SOECs), polymer electrolyte membrane cells (PEM) and alkaline electrolysis cells (AECs).[26] Traditionally, alkaline electrolysers are cheaper in terms of investment (they generally use nickel catalysts), but less-efficient; PEM electrolysers, conversely, are more expensive (they generally use expensive platinum group metal catalysts) but are more efficient and can operate at higher current densities, and can therefore be possibly cheaper if the hydrogen production is large enough.[27]
SOECs operate at high temperatures, typically around 800 °C (1,500 °F). At these high temperatures, a significant amount of the energy required can be provided as thermal energy (heat), and as such is termed high-temperature electrolysis. The heat energy can be provided from a number of different sources, including waste industrial heat, nuclear power stations or concentrated solar thermal plants. This has the potential to reduce the overall cost of the hydrogen produced by reducing the amount of electrical energy required for electrolysis.[28][29][30][31]
PEM electrolysis cells typically operate below 100 °C (212 °F).[28] These cells have the advantage of being comparatively simple and can be designed to accept widely varying voltage inputs, which makes them ideal for use with renewable sources of energy such as photovoltaic solar panels.[32] AECs optimally operate at high concentrations of electrolyte (KOH or potassium carbonate) and at high temperatures, often near 200 °C (392 °F).
Industrial output and efficiency
Efficiency of modern hydrogen generators is measured by energy consumed per standard volume of hydrogen (MJ/m3), assuming standard temperature and pressure of the H2. The lower the energy used by a generator, the higher would be its efficiency; a 100%-efficient electrolyser would consume 39.4 kilowatt-hours per kilogram (142 MJ/kg) of hydrogen,[33] 12,749 joules per litre (12.75 MJ/m3). Practical electrolysis typically uses a rotating electrolyser, where centrifugal force helps separate gas bubbles from water.[34] Such an electrolyser at 15 bar pressure may consume 50 kilowatt-hours per kilogram (180 MJ/kg), and a further 15 kilowatt-hours (54 MJ) if the hydrogen is compressed for use in hydrogen cars.[35]
Conventional alkaline electrolysis has an efficiency of about 70%,[36] however advanced alkaline water electrolysers with efficiency of up to 82% are available.[37] Accounting for the use of the higher heat value (because inefficiency via heat can be redirected back into the system to create the steam required by the catalyst), average working efficiencies for PEM electrolysis are around 80%, or 82% using the most modern alkaline electrolysers.[38]
PEM efficiency is expected to increase to approximately 86%[39] before 2030. Theoretical efficiency for PEM electrolysers is predicted up to 94%.[40]
_at_varying_natural_gas_prices.jpg.webp)
As of 2020, the cost of hydrogen by electrolysis is around $3–8/kg.[41] Considering the industrial production of hydrogen, and using current best processes for water electrolysis (PEM or alkaline electrolysis) which have an effective electrical efficiency of 70–82%,[42][43][44] producing 1 kg of hydrogen (which has a specific energy of 143 MJ/kg or about 40 kWh/kg) requires 50–55 kWh of electricity. At an electricity cost of $0.06/kWh, as set out in the Department of Energy hydrogen production targets for 2015,[45] the hydrogen cost is $3/kg.
The US DOE target price for hydrogen in 2020 is $2.30/kg, requiring an electricity cost of $0.037/kWh, which is achievable given recent PPA tenders for wind and solar in many regions.[46] The report by IRENA.ORG is an extensive factual report of present-day industrial hydrogen production consuming about 53 to 70 kWh per kg could go down to about 45 kWh/kg H
2.[47] The thermodynamic energy required for hydrogen by electrolysis translates to 33 kWh/kg, which is higher than steam reforming with carbon capture and higher than methane pyrolysis.
One of the advantages of electrolysis over hydrogen from steam methane reforming (SMR) is that the hydrogen can be produced on-site, meaning that the costly process of delivery via truck or pipeline is avoided.
Chemically assisted electrolysis
In addition to reduce the voltage required for electrolysis via the increasing of the temperature of the electrolysis cell it is also possible to electrochemically consume the oxygen produced in an electrolyser by introducing a fuel (such as carbon/coal,[48] methanol,[49][50] ethanol,[51] formic acid,[52] glycerol,[52] etc.) into the oxygen side of the reactor. This reduces the required electrical energy and has the potential to reduce the cost of hydrogen to less than 40~60% with the remaining energy provided in this manner.[53]
Carbon/hydrocarbon assisted water electrolysis (CAWE) has the potential to offer a less energy intensive, cleaner method of using chemical energy in various sources of carbon, such as low-rank and high sulfur coals, biomass, alcohols and methane (Natural Gas), where pure CO2 produced can be easily sequestered without the need for separation.[54][55]
Radiolysis
Nuclear radiation can break water bonds through radiolysis.[56][57] In the Mponeng gold mine, South Africa, researchers found bacteria in a naturally occurring high radiation zone. The bacterial community which was dominated by a new phylotype of Desulfotomaculum, was feeding on primarily radiolytically produced hydrogen.[58]
Thermolysis
Water spontaneously dissociates at around 2500 °C, but this thermolysis occurs at temperatures too high for usual process piping and equipment resulting in a rather low commercialization potential.[59]
Pyrolysis on biomass
Pyrolysis can be divided into different types based on the pyrolysis temperature, namely low-temperature slow pyrolysis, medium-temperature rapid pyrolysis, and high-temperature flash pyrolysis.[60] The source energy is mainly solar energy, with help of photosynthetic microorganisms to decompose water or biomass to produce hydrogen. However, this process has relatively low hydrogen yields and high operating cost. It is not a feasible method for industry.
Nuclear-assisted thermolysis
The high-temperature gas-cooled reactor (HTGR) is one of the most promising CO2-free nuclear technique to produce hydrogen by splitting water in a large scale. In this method, iodine-sulfur (IS) thermo-chemical cycle for splitting water and high-temperature steam electrolysis (HTSE) were selected as the main processes for nuclear hydrogen production. The S-I cycle follows three chemical reactions:[61]
Bunsen reaction: I2+SO2+2H2O=H2SO4+2HI
HI decomposition: 2HI=H2+I2
Sulfuric acid decomposition: H2SO4=SO2+1/2O2+H2O
The hydrogen production rate of HTGR with IS cycle is approximately 0.68 kg/s, and the capital cost to build a unit of power plant is $100 million.
Thermochemical cycle
Thermochemical cycles combine solely heat sources (thermo) with chemical reactions to split water into its hydrogen and oxygen components.[62] The term cycle is used because aside from water, hydrogen and oxygen, the chemical compounds used in these processes are continuously recycled. If electricity is partially used as an input, the resulting thermochemical cycle is defined as a hybrid one.
The sulfur-iodine cycle (S-I cycle) is a thermochemical cycle processes which generates hydrogen from water with an efficiency of approximately 50%. The sulfur and iodine used in the process are recovered and reused, and not consumed by the process. The cycle can be performed with any source of very high temperatures, approximately 950 °C, such as by Concentrating solar power systems (CSP) and is regarded as being well suited to the production of hydrogen by high-temperature nuclear reactors,[63] and as such, is being studied in the High-temperature engineering test reactor in Japan.[64][65][66][67] There are other hybrid cycles that use both high temperatures and some electricity, such as the Copper–chlorine cycle, it is classified as a hybrid thermochemical cycle because it uses an electrochemical reaction in one of the reaction steps, it operates at 530 °C and has an efficiency of 43 percent.[68]
Ferrosilicon method
Ferrosilicon is used by the military to quickly produce hydrogen for balloons. The chemical reaction uses sodium hydroxide, ferrosilicon, and water. The generator is small enough to fit a truck and requires only a small amount of electric power, the materials are stable and not combustible, and they do not generate hydrogen until mixed.[69] The method has been in use since World War I. A heavy steel pressure vessel is filled with sodium hydroxide and ferrosilicon, closed, and a controlled amount of water is added; the dissolving of the hydroxide heats the mixture to about 93 °C and starts the reaction; sodium silicate, hydrogen and steam are produced.[70]
Photobiological water splitting

Biological hydrogen can be produced in an algae bioreactor.[71] In the late 1990s it was discovered that if the algae are deprived of sulfur it will switch from the production of oxygen, i.e. normal photosynthesis, to the production of hydrogen. It seems that the production is now economically feasible by surpassing the 7–10 percent energy efficiency (the conversion of sunlight into hydrogen) barrier.[72] with a hydrogen production rate of 10–12 ml per liter culture per hour.[73]
Photocatalytic water splitting
The conversion of solar energy to hydrogen by means of water splitting process is one of the most interesting ways to achieve clean and renewable energy systems. However, if this process is assisted by photocatalysts suspended directly in water instead of using photovoltaic and an electrolytic system the reaction is in just one step, it can be made more efficient.[74][75][76] Current systems, however have low performance for commercial implementation.[77][78]
Biohydrogen routes
Biomass and waste streams can in principle be converted into biohydrogen with biomass gasification, steam reforming, or biological conversion like biocatalysed electrolysis[53] or fermentative hydrogen production.[1]
Among hydrogen production methods biological routes are potentially less energy intensive. In addition, a wide variety of waste and low-value materials such as agricultural biomass as renewable sources can be utilized to produce hydrogen via biochemical or thermochemical pathways.[79] Nevertheless, at present hydrogen is produced mainly from fossil fuels, in particular, natural gas which are non-renewable sources. Hydrogen is not only the cleanest fuel but also widely used in a number of industries, especially fertilizer, petrochemical and food ones.[80]
Biochemical routes to hydrogen are classified as dark and photo fermentation processes. In dark fermentation, carbohydrates are converted to hydrogen by fermentative microorganisms including strict anaerobe and facultative anaerobic bacteria. A theoretical maximum of 4 mol H2/mol glucose can be produced. Sugars are convertible to volatile fatty acids (VFAs) and alcohols as by-products during this process. Photo fermentative bacteria are able to generate hydrogen from VFAs. Hence, metabolites formed in dark fermentation can be used as feedstock in photo fermentation to enhance the overall yield of hydrogen.[80]
Fermentative hydrogen production
Fermentative hydrogen production converts organic substrates to hydrogen. A diverse group of bacteria promote this transformation. Photofermentation differs from dark fermentation because it only proceeds in the presence of light. For example, photo-fermentation with Rhodobacter sphaeroides SH2C can be employed to convert some fatty acids into hydrogen.[81]
Fermentative hydrogen production can be done using direct biophotolysis by green algae, indirect biophotolysis by cyanobacteria, photo-fermentation by anaerobic photosynthetic bacteria and dark fermentation by anaerobic fermentative bacteria. For example, studies on hydrogen production using H. salinarium, an anaerobic photosynthetic bacteria, coupled to a hydrogenase donor like E. coli, are reported in literature.[82] Enterobacter aerogenes is another hydrogen producer.[83]
Enzymatic hydrogen generation
Diverse enzymatic pathways have been designed to generate hydrogen from sugars.[84]
Biocatalysed electrolysis

Besides dark fermentation, electrohydrogenesis (electrolysis using microbes) is another possibility. Using microbial fuel cells, wastewater or plants can be used to generate power. Biocatalysed electrolysis should not be confused with biological hydrogen production, as the latter only uses algae and with the latter, the algae itself generates the hydrogen instantly, where with biocatalysed electrolysis, this happens after running through the microbial fuel cell and a variety of aquatic plants[85] can be used. These include reed sweetgrass, cordgrass, rice, tomatoes, lupines and algae.[86]

Nanogalvanic aluminum alloy powder
Aluminum alloy powder reacts with water to produce hydrogen gas upon contact with water. It reportedly generates hydrogen at 100 percent of the theoretical yield.[87][88] Cost-effective routes for generating the aluminum alloy remain elusive.
CC-HOD
CC-HOD (Catalytic Carbon - Hydrogen On Demand) is a low-temperature process in which carbon and aluminium are submerged and heated to about 80 °C (176 °F), causing a chemical reaction which produces hydrogen.
Natural hydrogen
Hydrogen is also present naturally underground. This natural hydrogen, also called white hydrogen, can be extracted from wells in a similar manner as fossil fuels such as oil and natural gas.[89][90]
White hydrogen could be found or produced in the Mid-continental Rift System at scale for a renewable hydrogen economy. Water could be pumped down to hot iron-rich rock to produce hydrogen and the hydrogen could be extracted.[91]
Environmental impact
As of 2020, most hydrogen is produced from fossil fuels, resulting in carbon dioxide emissions.[92] Hydrogen produced by this technology has been described as grey hydrogen when emissions are released to the atmosphere, and blue hydrogen when emissions are captured through carbon capture and storage (CCS).[93][94] Blue hydrogen has been estimated to have a carbon footprint 20% greater than burning gas or coal for heat and 60% greater when compared to burning diesel for heat, assuming US up- and mid-stream methane leakage rates and production via steam methane reformers (SMR) retrofitted with carbon dioxide capture.[95]
The use of autothermal reformers (ATR) with integrated capture of carbon dioxide allows higher capture rates at satisfactory energy efficiencies and life cycle assessments have shown lower greenhouse gas emissions for such plants compared to SMRs with carbon dioxide capture.[96] Application of ATR technology with integrated capture of carbon dioxide in Europe has been assessed to have a lower greenhouse gas footprint than burning natural gas, e.g. for the H21 project with a reported reduction of 68% due to a reduced carbon dioxide intensity of natural gas combined with a more suitable reactor type for capture of carbon dioxide.[97]
Hydrogen produced from renewable energy sources is often referred to as green hydrogen. Two ways of producing hydrogen from renewable energy sources are claimed to be practical. One is to use power to gas, in which electric power is used to produce hydrogen from electrolysis of water, and the other is to use landfill gas to produce hydrogen in a steam reformer. Hydrogen fuel, when produced by renewable sources of energy like wind or solar power, is a renewable fuel.[98][99] Hydrogen produced from nuclear energy via electrolysis is sometimes viewed as a subset of green hydrogen, but can also be referred to as pink hydrogen. The Oskarshamn Nuclear Power Plant made an agreement in January 2022 to supply commercial pink hydrogen in the order of kilograms per day.[100]
As of 2020, estimated costs of production are $1–1.80/kg for grey hydrogen and blue hydrogen,[101] and $2.50–6.80 for green hydrogen.[101]
94 million tonnes of grey hydrogen are produced globally using fossil fuels as of 2022, primarily natural gas, and are therefore a significant source of greenhouse gas emissions.[102][103][104][105]
Hydrogen uses
Hydrogen is used for the conversion of heavy petroleum fractions into lighter ones via hydrocracking. It is also used in other processes including the aromatization process, hydrodesulfurization and the production of ammonia via the Haber process, the primary industrial method for the production of synthetic nitrogen fertilizer for growing 47 percent of food worldwide.[106]
Hydrogen may be used in fuel cells for local electricity generation or potentially as a transportation fuel.
Hydrogen is produced as a by-product of industrial chlorine production by electrolysis. Although requiring expensive technologies, hydrogen can be cooled, compressed and purified for use in other processes on site or sold to a customer via pipeline, cylinders or trucks. The discovery and development of less expensive methods of production of bulk hydrogen is relevant to the establishment of a hydrogen economy.[1]
See also

- Ammonia production
- Artificial photosynthesis
- Biohydrogen
- Hydrogen analyzer
- Hydrogen compressor
- Hydrogen economy § Color codes
- Hydrogen embrittlement
- Hydrogen leak testing
- Hydrogen pipeline transport
- Hydrogen purifier
- Hydrogen purity
- Hydrogen safety
- Hydrogen sensor
- Hydrogen storage
- Hydrogen station
- Hydrogen tank
- Hydrogen tanker
- Hydrogen technologies
- Hydrogen valve
- Industrial gas
- Liquid hydrogen
- Next Generation Nuclear Plant (partly for hydrogen production)
- Hy4Heat
- Lane hydrogen producer
- Linde–Frank–Caro process
- Underground hydrogen storage
References
- 1 2 3 Häussinger, Peter; Lohmüller, Reiner; Watson, Allan M. (2011). "Hydrogen, 1. Properties and Occurrence". Ullmann's Encyclopedia of Industrial Chemistry. doi:10.1002/14356007.a13_297.pub2. ISBN 978-3-527-30673-2.
- ↑ "Life cycle emissions of hydrogen". 4thgeneration.energy. Retrieved 2020-05-27.
- ↑ Energy, U. S. D. o. The Impact of Increased Use of Hydrogen on Petroleum Consumption and Carbon Dioxide Emissions. 84 (Energy Information Administration, Washington, DC, 2008)
- ↑ Collins, Leigh (2021-05-18). "A net-zero world 'would require 306 million tonnes of green hydrogen per year by 2050': IEA | Recharge". Recharge | Latest renewable energy news. Archived from the original on 2021-05-21.
- ↑ "Global Hydrogen Generation Market Size Report, 2030".
- ↑ Dincer, Ibrahim; Acar, Canan (2015). "Review and evaluation of hydrogen production methods for better sustainability". International Journal of Hydrogen Energy. 40 (34): 11096. doi:10.1016/j.ijhydene.2014.12.035. ISSN 0360-3199.
- 1 2 3 Press, Roman J.; Santhanam, K. S. V.; Miri, Massoud J.; Bailey, Alla V.; Takacs, Gerald A. (2008). Introduction to hydrogen Technology. John Wiley & Sons. p. 249. ISBN 978-0-471-77985-8.
- ↑ Collodi, Guido (2010-03-11). "Hydrogen Production via Steam Reforming with CO2 Capture" (PDF). CISAP4 4th International Conference on Safety and Environment in the Process Industry. Retrieved 2015-11-28.
- ↑ "HFCIT Hydrogen Production: Natural Gas Reforming". U.S. Department of Energy. 2008-12-15.
- ↑ "Hydrogen technologies". www.interstatetraveler.us.
- ↑
- ↑ "Kværner-process with plasma arc waste disposal technology". Archived from the original on 2014-03-13. Retrieved 2009-10-13.
- 1 2 Hordeski, M. F. Alternative fuels: the future of hydrogen. 171-199 (The Fairmont Press, inc., 2007).
- ↑ "Emissions Advantages of Gasification". National Energy Technology Laboratory. U.S. Department of Energy.
- ↑ "Emissions from burning coal". U.S. EIA. U.S. Energy Information Administration.
- ↑ Lee, Woon-Jae; Lee, Yong-Kuk (2001). "Internal Gas Pressure Characteristics Generated during Coal Carbonization in a Coke Oven". Energy & Fuels. 15 (3): 618–23. doi:10.1021/ef990178a.
- ↑ Gemayel, Jimmy El; MacChi, Arturo; Hughes, Robin; Anthony, Edward John (2014). "Simulation of the integration of a bitumen upgrading facility and an IGCC process with carbon capture". Fuel. 117: 1288–97. doi:10.1016/j.fuel.2013.06.045.
- ↑ Blain, Loz (2022-10-04). "Oil-eating microbes excrete the world's cheapest "clean" hydrogen". New Atlas. Retrieved 2022-10-06.
- ↑ Petrova, Magdalena (2020-12-04). "Green hydrogen is gaining traction, but still has massive hurdles to overcome". CNBC. Retrieved 2021-06-20.
- ↑ "ITM - Hydrogen Refuelling Infrastructure - February 2017" (PDF). level-network.com. Retrieved 17 April 2018.
- ↑ "Cost reduction and performance increase of PEM electrolysers" (PDF). fch.europa.eu. Fuel Cells and Hydrogen Joint Undertaking. Retrieved 17 April 2018.
- ↑ Kalamaras, Christos M.; Efstathiou, Angelos M. (2013). "Hydrogen Production Technologies: Current State and Future Developments". Conference Papers in Energy. 2013: 1–9. doi:10.1155/2013/690627.
- ↑ "Cost reduction and performance increase of PEM electrolysers" (PDF). fch.europa.eu. Fuel Cell and Hydrogen Joint Undertaking. Retrieved 17 April 2018.
- ↑ "Report and Financial Statements 30 April 2016" (PDF). itm-power.com. Retrieved 17 April 2018.
- ↑ "Hydrogen Production: Natural Gas Reforming". energy.gov. US Department of Energy. Retrieved 17 April 2018.
- ↑ Badwal, Sukhvinder P.S.; Giddey, Sarbjit; Munnings, Christopher (2013). "Hydrogen production via solid electrolytic routes". Wiley Interdisciplinary Reviews: Energy and Environment. 2 (5): 473–487. doi:10.1002/wene.50. S2CID 135539661.
- ↑ Sebbahi, Seddiq; Nabil, Nouhaila; et al. (2022). "Assessment of the three most developed water electrolysis technologies: Alkaline Water Electrolysis, Proton Exchange Membrane and Solid-Oxide Electrolysis". Materials Today: Proceedings. 66: 140–145. doi:10.1016/j.matpr.2022.04.264. ISSN 2214-7853. S2CID 248467810.
- 1 2 Ogden, J.M. (1999). "Prospects for building a hydrogen energy infrastructure". Annual Review of Energy and the Environment. 24: 227–279. doi:10.1146/annurev.energy.24.1.227.
- ↑ Hauch, Anne; Ebbesen, Sune Dalgaard; Jensen, Søren Højgaard; Mogensen, Mogens (2008). "Highly efficient high temperature electrolysis". Journal of Materials Chemistry. 18 (20): 2331–40. doi:10.1039/b718822f.
- ↑ In the laboratory, water electrolysis can be done with a simple apparatus like a Hofmann voltameter:"Electrolysis of water and the concept of charge". Archived from the original on 2010-06-13.
- ↑ "Nuclear power plants can produce hydrogen to fuel the 'hydrogen economy'" (Press release). American Chemical Society. March 25, 2012. Archived from the original on December 10, 2019. Retrieved March 9, 2013.
- ↑ Clarke, R.E.; Giddey, S.; Ciacchi, F.T.; Badwal, S.P.S.; Paul, B.; Andrews, J. (2009). "Direct coupling of an electrolyser to a solar PV system for generating hydrogen". International Journal of Hydrogen Energy. 34 (6): 2531–42. doi:10.1016/j.ijhydene.2009.01.053.
- ↑ Luca Bertuccioli; et al. (7 February 2014). "Development of water electrolysis in the European Union" (PDF). Client Fuel Cells and Hydrogen Joint Undertaking. Archived from the original (PDF) on 31 March 2015. Retrieved 2 May 2018.
- ↑ L. Lao; C. Ramshaw; H. Yeung (2011). "Process intensification: water electrolysis in a centrifugal acceleration field". Journal of Applied Electrochemistry. 41 (6): 645–656. doi:10.1007/s10800-011-0275-2. hdl:1826/6464. S2CID 53760672. Retrieved June 12, 2011.
- ↑ Stensvold, Tore (26 January 2016). «Coca-Cola-oppskrift» kan gjøre hydrogen til nytt norsk industrieventyr. Teknisk Ukeblad, .
- ↑ Stolten, Detlef (Jan 4, 2016). Hydrogen Science and Engineering: Materials, Processes, Systems and Technology. John Wiley & Sons. p. 898. ISBN 9783527674299. Retrieved 22 April 2018.
- ↑ thyssenkrupp. "Hydrogen from water electrolysis - solutions for sustainability". thyssenkrupp-uhde-chlorine-engineers.com. Archived from the original on 19 July 2018. Retrieved 28 July 2018.
- ↑ "ITM - Hydrogen Refuelling Infrastructure - February 2017" (PDF). level-network.com. Retrieved 17 April 2018.
- ↑ "Cost reduction and performance increase of PEM electrolysers" (PDF). fch.europa.eu. Fuel Cells and Hydrogen Joint Undertaking. Retrieved 17 April 2018.
- ↑ Bjørnar Kruse; Sondre Grinna; Cato Buch (13 February 2002). "Hydrogen—Status and Possibilities" (PDF). The Bellona Foundation. p. 20. Archived from the original on 16 September 2013.
{{cite web}}
: CS1 maint: unfit URL (link) - ↑ Fickling, David (2 December 2020). "Hydrogen Is a Trillion Dollar Bet on the Future". Bloomberg.com. Archived from the original on 2 December 2020.
green hydrogen .. current pricing of around $3 to $8 a kilogram .. gray hydrogen, which costs as little as $1
- ↑ Werner Zittel; Reinhold Wurster (1996-07-08). "Chapter 3: Production of Hydrogen. Part 4: Production from electricity by means of electrolysis". HyWeb: Knowledge - Hydrogen in the Energy Sector. Ludwig-Bölkow-Systemtechnik GmbH.
- ↑ Bjørnar Kruse; Sondre Grinna; Cato Buch (2002-02-13). "Hydrogen—Status and Possibilities". The Bellona Foundation. Archived from the original (PDF) on 2011-07-02.
Efficiency factors for PEM electrolysers up to 94% are predicted, but this is only theoretical at this time.
- ↑ "high-rate and high efficiency 3D water electrolysis". Grid-shift.com. Archived from the original on 2012-03-22. Retrieved 2011-12-13.
- ↑ "DOE Technical Targets for Hydrogen Production from Electrolysis". energy.gov. US Department of Energy. Retrieved 22 April 2018.
- ↑ Deign, Jason. "Xcel Attracts 'Unprecedented' Low Prices for Solar and Wind Paired With Storage". greentechmedia.com. Wood MacKenzie. Retrieved 22 April 2018.
- ↑ accessed June 22, 2021
- ↑ Giddey, S; Kulkarni, A; Badwal, S.P.S (2015). "Low emission hydrogen generation through carbon assisted electrolysis". International Journal of Hydrogen Energy. 40 (1): 70–4. doi:10.1016/j.ijhydene.2014.11.033.
- ↑ Uhm, Sunghyun; Jeon, Hongrae; Kim, Tae Jin; Lee, Jaeyoung (2012). "Clean hydrogen production from methanol–water solutions via power-saved electrolytic reforming process". Journal of Power Sources. 198: 218–22. doi:10.1016/j.jpowsour.2011.09.083.
- ↑ Ju, Hyungkuk; Giddey, Sarbjit; Badwal, Sukhvinder P.S (2017). "The role of nanosized SnO2 in Pt-based electrocatalysts for hydrogen production in methanol assisted water electrolysis". Electrochimica Acta. 229: 39–47. doi:10.1016/j.electacta.2017.01.106.
- ↑ Ju, Hyungkuk; Giddey, Sarbjit; Badwal, Sukhvinder P.S; Mulder, Roger J (2016). "Electro-catalytic conversion of ethanol in solid electrolyte cells for distributed hydrogen generation". Electrochimica Acta. 212: 744–57. doi:10.1016/j.electacta.2016.07.062.
- 1 2 Lamy, Claude; Devadas, Abirami; Simoes, Mario; Coutanceau, Christophe (2012). "Clean hydrogen generation through the electrocatalytic oxidation of formic acid in a Proton Exchange Membrane Electrolysis Cell (PEMEC)". Electrochimica Acta. 60: 112–20. doi:10.1016/j.electacta.2011.11.006.
- 1 2 Badwal, Sukhvinder P. S; Giddey, Sarbjit S; Munnings, Christopher; Bhatt, Anand I; Hollenkamp, Anthony F (2014). "Emerging electrochemical energy conversion and storage technologies". Frontiers in Chemistry. 2: 79. Bibcode:2014FrCh....2...79B. doi:10.3389/fchem.2014.00079. PMC 4174133. PMID 25309898.
- ↑ Ju, H; Badwal, S.P.S; Giddey, S (2018). "A comprehensive review of carbon and hydrocarbon assisted water electrolysis for hydrogen production". Applied Energy. 231: 502–533. doi:10.1016/j.apenergy.2018.09.125. S2CID 117669840.
- ↑ Ju, Hyungkuk; Badwal, Sukhvinder; Giddey, Sarbjit (2018). "A comprehensive review of carbon and hydrocarbon assisted water electrolysis for hydrogen production". Applied Energy. 231: 502–533. doi:10.1016/j.apenergy.2018.09.125. S2CID 117669840.
- ↑ An Introduction to Radiation Chemistry Chapter 7
- ↑ Nuclear Hydrogen Production Handbook Chapter 8
- ↑ Li-Hung Lin; Pei-Ling Wang; Douglas Rumble; Johanna Lippmann-Pipke; Erik Boice; Lisa M. Pratt; Barbara Sherwood Lollar; Eoin L. Brodie; Terry C. Hazen; Gary L. Andersen; Todd Z. DeSantis; Duane P. Moser; Dave Kershaw; T. C. Onstott (2006). "Long-Term Sustainability of a High-Energy, Low-Diversity Crustal Biome". Science. 314 (5798): 479–82. Bibcode:2006Sci...314..479L. doi:10.1126/science.1127376. PMID 17053150. S2CID 22420345.
- ↑ "Dream or Reality? Electrification of the Chemical Process Industries". www.aiche-cep.com. Retrieved 2021-08-22.
- ↑ Guoxin, Hu; Hao, Huang (May 2009). "Hydrogen rich fuel gas production by gasification of wet biomass using a CO2 sorbent". Biomass and Bioenergy. 33 (5): 899–906. doi:10.1016/j.biombioe.2009.02.006. ISSN 0961-9534.
- ↑ Ping, Zhang; Laijun, Wang; Songzhe, Chen; Jingming, Xu (2018-01-01). "Progress of nuclear hydrogen production through the iodine–sulfur process in China". Renewable and Sustainable Energy Reviews. 81: 1802–1812. doi:10.1016/j.rser.2017.05.275. ISSN 1364-0321.
- ↑ Producing hydrogen: The Thermochemical cycles
- ↑ IEA Energy Technology Essentials - Hydrogen Production & Distribution Archived 2011-11-03 at the Wayback Machine, April 2007
- ↑ "HTTR High Temperature engineering Test Reactor". Httr.jaea.go.jp. Archived from the original on 2014-02-03. Retrieved 2014-01-23.
- ↑ https://smr.inl.gov/Document.ashx?path=DOCS%2FGCR-Int%2FNHDDELDER.pdf Archived 2016-12-21 at the Wayback Machine. Progress in Nuclear Energy Nuclear heat for hydrogen production: Coupling a very high/high temperature reactor to a hydrogen production plant. 2009
- ↑ "Status report 101 - Gas Turbine High Temperature Reactor (GTHTR300C)" (PDF).
- ↑ "JAEA'S VHTR FOR HYDROGEN AND ELECTRICITY COGENERATION: GTHTR300C" (PDF). Archived from the original (PDF) on 2017-08-10. Retrieved 2013-12-04.
- ↑ Chukwu, C., Naterer, G. F., Rosen, M. A., "Process Simulation of Nuclear-Produced Hydrogen with a Cu-Cl Cycle", 29th Conference of the Canadian Nuclear Society, Toronto, Ontario, Canada, June 1–4, 2008. "Process Simulation of Nuclear-Based Thermochemical Hydrogen Production with a Copper-Chlorine Cycle" (PDF). Archived from the original (PDF) on 2012-02-20. Retrieved 2013-12-04.
- ↑ Report No 40: The ferrosilicon process for the generation of hydrogen
- ↑ Candid science: conversations with famous chemists, István Hargittai, Magdolna Hargittai, p. 261, Imperial College Press (2000) ISBN 1-86094-228-8
- ↑ Hemschemeier, Anja; Melis, Anastasios; Happe, Thomas (2009). "Analytical approaches to photobiological hydrogen production in unicellular green algae". Photosynthesis Research. 102 (2–3): 523–40. doi:10.1007/s11120-009-9415-5. PMC 2777220. PMID 19291418.
- ↑ "DOE 2008 Report 25 %" (PDF).
- ↑ Jenvanitpanjakul, Peesamai (February 3–4, 2010). Renewable Energy Technology And Prospect On Biohydrogen Study In Thailand (PDF). Steering Committee Meeting and Workshop of APEC Research Network for Advanced Biohydrogen Technology. Taichung: Feng Chia University. Archived from the original (PDF) on July 4, 2013.
- ↑ Navarro Yerga, Rufino M.; Álvarez Galván, M. Consuelo; Del Valle, F.; Villoria De La Mano, José A.; Fierro, José L. G. (2009). "Water Splitting on Semiconductor Catalysts under Visible-Light Irradiation". ChemSusChem. 2 (6): 471–85. doi:10.1002/cssc.200900018. PMID 19536754.
- ↑ Navarro, R.M.; Del Valle, F.; Villoria De La Mano, J.A.; Álvarez-Galván, M.C.; Fierro, J.L.G. (2009). "Photocatalytic Water Splitting Under Visible Light: Concept and Catalysts Development". Photocatalytic Technologies. Advances in Chemical Engineering. Vol. 36. pp. 111–43. doi:10.1016/S0065-2377(09)00404-9. ISBN 978-0-12-374763-1.
- ↑ Ropero-Vega, J.L.; Pedraza-Avella, J.A.; Niño-Gómez, M.E. (September 2015). "Hydrogen production by photoelectrolysis of aqueous solutions of phenol using mixed oxide semiconductor films of Bi–Nb–M–O (M=Al, Fe, Ga, In) as photoanodes". Catalysis Today. 252: 150–156. doi:10.1016/j.cattod.2014.11.007.
- ↑ Low, Jingxiang; Yu, Jiaguo; Jaroniec, Mietek; Wageh, Swelm; Al‐Ghamdi, Ahmed A. (May 2017). "Heterojunction Photocatalysts". Advanced Materials. 29 (20). doi:10.1002/adma.201601694. ISSN 0935-9648.
- ↑ Djurišić, Aleksandra B.; He, Yanling; Ng, Alan M. C. (2020-03-01). "Visible-light photocatalysts: Prospects and challenges". APL Materials. 8 (3). doi:10.1063/1.5140497. ISSN 2166-532X.
- ↑ Sasidhar, Nallapaneni (November 2023). "Carbon Neutral Fuels and Chemicals from Standalone Biomass Refineries" (PDF). Indian Journal of Environment Engineering. 3 (2): 1–8. doi:10.54105/ijee.B1845.113223. ISSN 2582-9289. S2CID 265385618. Retrieved 29 December 2023.
- 1 2 Asadi, Nooshin; Karimi Alavijeh, Masih; Zilouei, Hamid (2017). "Development of a mathematical methodology to investigate biohydrogen production from regional and national agricultural crop residues: A case study of Iran". International Journal of Hydrogen Energy. 42 (4): 1989–2007. doi:10.1016/j.ijhydene.2016.10.021.
- ↑ Tao, Y; Chen, Y; Wu, Y; He, Y; Zhou, Z (2007). "High hydrogen yield from a two-step process of dark- and photo-fermentation of sucrose". International Journal of Hydrogen Energy. 32 (2): 200–6. doi:10.1016/j.ijhydene.2006.06.034.
- ↑ Rajanandam, Brijesh; Kiran, Siva (2011). "Optimization of hydrogen production by Halobacterium salinarium coupled with E coli using milk plasma as fermentative substrate". Journal of Biochemical Technology. 3 (2): 242–4. Archived from the original on 2013-07-31. Retrieved 2013-03-09.
- ↑ Asadi, Nooshin; Zilouei, Hamid (March 2017). "Optimization of organosolv pretreatment of rice straw for enhanced biohydrogen production using Enterobacter aerogenes". Bioresource Technology. 227: 335–344. doi:10.1016/j.biortech.2016.12.073. PMID 28042989.
- ↑ Percival Zhang, Y-H; Sun, Jibin; Zhong, Jian-Jiang (2010). "Biofuel production by in vitro synthetic enzymatic pathway biotransformation". Current Opinion in Biotechnology. 21 (5): 663–9. doi:10.1016/j.copbio.2010.05.005. PMID 20566280.
- ↑ Strik, David P. B. T. B.; Hamelers (Bert), H. V. M.; Snel, Jan F. H.; Buisman, Cees J. N. (2008). "Green electricity production with living plants and bacteria in a fuel cell". International Journal of Energy Research. 32 (9): 870–6. doi:10.1002/er.1397. S2CID 96849691.
- "Living plants produce energy". Wageningen University and Research Centre (Press release). Archived from the original on 2010-05-17.
- ↑ Timmers, Ruud (2012). Electricity generation by living plants in a plant microbial fuel cell (PhD Thesis). Wageningen University. ISBN 978-94-6191-282-4.
- ↑ "Aluminum Based Nanogalvanic Alloys for Hydrogen Generation". U.S. Army Combat Capabilities Development Command Army Research Laboratory. Retrieved January 6, 2020.
- ↑ McNally, David (July 25, 2017). "Army discovery may offer new energy source". U.S. Army. Retrieved January 6, 2020.
- ↑ Gaucher, Éric C. (February 2020). "New Perspectives in the Industrial Exploration for Native Hydrogen". Elements: An International Magazine of Mineralogy, Geochemistry, and Petrology. 16 (1): 8-9. doi:10.2138/gselements.16.1.8.
- ↑ Hand, Eric. "Hidden hydrogen". science.org. Science. Retrieved 9 December 2023.
- ↑ https://www.usgs.gov/news/featured-story/potential-geologic-hydrogen-next-generation-energy
- ↑ Rapier, Robert (May 26, 2020). "Life Cycle Emissions of Hydrogen Climate". 4thgeneration.energy. Retrieved 2023-12-12.
- ↑ Hessler, Uwe (December 6, 2020). "First element in periodic table: Why all the fuss about hydrogen?". dw.com. Deutsche Welle.
- ↑ "Air Products to Build Europe’s Largest Blue Hydrogen Plant and Strengthens Long-term Agreement", Air Products press release, November 6, 2023. Retrieved 2023-11-14.
- ↑ Robert W. Howarth; Mark Z. Jacobson (12 August 2021). "How green is blue hydrogen?". Energy Science & Engineering. doi:10.1002/ESE3.956. ISSN 2050-0505. Wikidata Q108067259.
- ↑ Antonini, Cristina, et al. "Hydrogen production from natural gas and biomethane with carbon capture and storage – A techno-environmental analysis", Sustainable Energy & Fuels, Royal Society of Chemistry, 2020. Confirmed 2023-12-12.
- ↑ "Facts on low-carbon hydrogen – A European perspective", ZEP Oct 2021. Confirmed 2023-12-12.
- ↑ "New Horizons for Hydrogen" (PDF). Research Review. National Renewable Energy Laboratory (2): 2–9. April 2004.
- ↑ Dvorak, Phred, "WSJ News Exclusive: Green Hydrogen Gets a Boost in the U.S. With $4 Billion Plant: The planned factory, a joint venture by Air Products and AES ..."], Wall Street Journal, December 8, 2022. Retrieved 2023-11-14. (subscription required)
- ↑ Collins, Leigh (25 January 2022). "World first for nuclear-powered pink hydrogen as commercial deal signed in Sweden | Recharge". Recharge | Latest renewable energy news.
- 1 2 Collins, Leigh (19 March 2020). "A wake-up call on green hydrogen: the amount of wind and solar needed is immense | Recharge". Recharge | Latest renewable energy news. Archived from the original on 4 June 2021.
- ↑ "How does the energy crisis affect the transition to net zero?". European Investment Bank. Retrieved 2022-12-23.
- ↑ "Hydrogen - Fuels & Technologies". IEA. Retrieved 2022-12-23.
- ↑ Castelvecchi, Davide (2022-11-16). "How the hydrogen revolution can help save the planet — and how it can't". Nature. 611 (7936): 440–443. doi:10.1038/d41586-022-03699-0. PMID 36385542. S2CID 253525130.
- ↑ "Hydrogen". energy.ec.europa.eu. Retrieved 2022-12-23.
- ↑ Ritchie, Hannah. "How many people does synthetic fertilizer feed?". Our World in Data. Global Change Data Lab. Retrieved 16 September 2021.
Further reading
- Francesco Calise; et al., eds. (2019). Solar Hydrogen Production. Academic Press. ISBN 978-0-12-814853-2.