
Post-tensioned stone is a high-performance composite construction material: stone held in compression with tension elements. The tension elements can be connected to the outside of the stone, but more typically uses tendons threaded internally through a duct formed from aligned drilled holes.
Post-tensioned stone ("PT stone") could consist of a single piece, but drill limitations and other considerations mean it is typically an assembly of multiple components with mortar between pieces. PT stone has been used in both vertical columns (posts), and in horizontal beams (lintels). It has also been used in more unusual stonemasonry engineering applications: arch stabilization, flexible foot bridges, and cantilevered sculptures.
A closely related method is pre-tensioned stone.[1] A duct is drilled into the stone is used to host a steel rod held in tension with jacks while the duct is filled with epoxy grout. After the epoxy has set, the ends of the rod can be released from the jacks, placing the stone under compression. Similar to pre-stressed concrete, the pre- and post-tensioned methods can be used in different contexts.
Post-tensioned stone also has a close affiliation with massive precut stone, which is the central technique of modern load-bearing stonemasonry.
Rationale

"Post-tensioned stone increases the failure load of stone in bending, but also the stiffness of a structure by reducing joint cracking. This method of construction is widely used for concrete structures, but the advantages of using similar techniques with stone are only just being realised.".[2]
Stone has great compressive strength, so is ideal in compressive structures like stone arches. [3] However, it has relatively weak flexural strength (compared to steel or wood), so in isolation cannot be safely used in wide spans under tension.[3]
For concrete, this problem has been long solved: in addition to conventional tensile reinforcement, engineers developed prestressed concrete methods starting around 1888. Such tension-reinforced concrete applications combine compressive strength with pre-stressed tensile compresssion for combined strength much greater than either of the individual components, and have been in wide use for decades. One of the early concrete engineers Eugène Freyssinet improved concrete pre-stressing methods, and it is claimed that he also applied post-tensioned concrete methods to stone.[4] As for concrete, post-tensioning maintains stone in compression, thereby increasing its strength.
Post-tensioning is achieved steel tendons either threaded through ducts within the stone elements or along their surface. Once the stone components are in place, the tendons are tensioned using hydraulic jacks, and the force is transferred to the stone through anchorages located at the ends of the tendons. The tensioning process imparts a compressive force to the stone, which improves its capacity to resist tensile stresses that could otherwise cause cracking or failure.
Energy use and carbon emissions
Stone is 'natural precast concrete' so only needs to be cut (and strength tested) and post-tensioned prior to use in construction. Compared to concrete and steel, post-tensioned stone production has dramatically lower energy costs, with concomitant lower carbon emissions.[5]
Potential for applications
.jpg.webp)
Post-tensioned stone has potential to replace steel-reinforced concrete in some contexts, as, according to structural engineer Steve Webb "a post-tensioned stone beam is as strong as steel”.[6] "Post-tensioning offers new potential for the revival of masonry as a structural material".[7] Post-tensioned stone has the potential to be used in conjunction with massive precut stone in a range of designs.
In 2020, post-tensioned stone was featured prominently in "The New Stone Age" an exhibition at The Building Centre.[8]
Architect James Simpson writes: "The term 'engineered timber' is already commonly used in construction, so why not a structural 'engineered stone'? ... The most exciting possibility for the stone industry... is the possible creation of a system of engineered stone for framed, or partly framed, structures. This would exploit the compressive strength of stone, which can be greater than that of concrete, combined with post-tensioning by stainless steel rods. Walls, columns, beams and slabs could all be made from small pieces of factory-sawn stone, cut and pre-drilled to a design of standard components."[9]
Benefits of post-tensioned stone preassembly
Structural benefits of PT stone
.jpg.webp)
Compared to reinforced concrete, post-tensioned stone has at least four advantages.[7][3]
- Reduced material usage. By enhancing the structural performance of stone, post-tensioning allows for the use of thinner stone slabs or walls, reducing the overall material requirements and associated costs.
- Slenderness. Less bulky beams, due to PT stone's greater strength compared to PT concrete.[3]
- Durability offered by the stone's resistant to weather conditions. This reduces maintenance costs.
- Aesthetics. Instead of cladding concrete in stone, the load-bearing stone has the appearance of stone .
- Reduced embedded carbon. Post-tensioned stone causes the emission of <1/3rd of carbon dioxide greenhouse gas relative to concrete.[3][10]
- Expanded design options. Post-tensioning provides additional design options, allowing architects, engineers, and sculptors to create more innovative and complex structures that would be difficult to achieve with traditional stone construction methods.
- Seismic Resilience. Compared to conventional stone, PT stone structures can have improved seismic performance, as the compressive forces could help to maintain the integrity of the structure during ground motion. This could in some cases be counterbalanced by the resilience of sliding stone components.
- Lower cost. A study of a 30-storey office block found that using PT stone floor panels was cheaper than concrete floors.[5]
Operational advantages of PT stone
Compared to conventional stonemasonry, post-tensioned stone has substantial structural and weight benefits.[11] In addition, compared to standard stonemasonry, post-tensioned stone preassembly has at least three operational advantages[12]
- Pre-assembly of the pieces can be done at ground level, reducing cost and improving safety.
- Easier review of the assembly, including testing strength and waterproofing of the mortar.
- Easier to schedule tasks, as the prefabricated post-tensioned stone assemblies can be stored before using.
Challenges facing PT stone adoption


The wide adoption of post-tensioned stone currently faces a number of challenges, including:
- Load-bearing stone's cultural affiliation with old-fashioned, low-tech architecture.
- Confusion with the use of cosmetic stone in high-end luxury construction and the perception of high cost.
- Limited knowledge amongst most structural engineers, beyond elite firms like Arup Group, Buro Happold, and Webb Yates. Structural engineering training does not include stone. This is changing with increased attention from the Institution of Structural Engineers[2]
- The absence of international standards for engineering with stone.
- Lack of stonemasons with knowledge of PT stone methods.
- Absence of a large-scale industry for pre-fabricated PT stone.
- By analogy with precast concrete, a lack of manufactured modular PT stone components.
- The high cost of some early high-profile post-tensioned stone projects, notably Portcullis House.
- Shortage of dimension-stone quarries that do routine strength testing and can give strength certificates for their stone components.
- The need to develop better CAD-CAM software and hardware for automated CNC stone cutting of precise shapes.
In the early 2020s, the dimension-stone industry in most countries was structured almost entirely for tiles and cladding.
History of post-tensioned stone construction
Post-tensioned stone has been used in a range of applications. After experimental use in the 1990s, its application increased in the early 2020s in part due to awareness of the high carbon emissions associated with concrete.
Post-tensioned stone footbridges with spans up to 40 m have been built in Japan, Switzerland, Germany, and Spain,[7] and are sold commercially in spans of up to 20 m by Kusser Granitwerke.
PT brick and concrete masonry
While post-tensioned stone has only been used in construction applications since the 1990s, post-tensioned masonry more generally dates back to at least the early 1800s: "In 1825 a posttensioning method for tunnelling under the River Thames was utilized in England. The project involved the construction of vertical tube caissons of 15m diameter and 21 m height. The 0.75m thick brick walls were reinforced and posttensioned with 25mm diameter wrought iron rods.".[13] In the mid-20th century, the Sydney Opera House shells were constructed from pre-cast concrete masonry beams that were assembled into the roofs using post-tensioning. By 1982, post-tensioned masonry was sufficiently widespread to fill a book published by the Institution of Civil Engineers, though this was brick and precast concrete masonry.[14] In 1985 and 1986, structural engineer Remo Pedreschi and others published studies of post-tensioned brick.[15]
PT stone in the 20th century
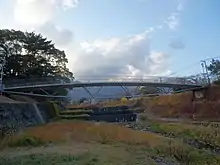
.jpg.webp)

- In 1947, the Compagnons du Devoir tested the concept of post-tensioned stone, finding that an 8 m span could support a 7-t load.[16]
- In the 1980s, Kluesner Engineering developed post-tensioned stone panels.[17]
"The advantages of posttensioned stone are much the same as for concrete. It permits the stone to carry larger loads over longer spans than would be possible with conventional units. The stone units can be plant-fabricated in much larger units to span column to column in the building. Window systems can be carried directly on the stone panels, thereby eliminating a separate window support system. … A few structural applications have been built using beams for such building features as porticoes, where the live loads have been limited to roof loads and wind loads.".[17]
- In the 1980s, the Rock of Ages Corporation developed Accu-Tensioned Granite Press Rolls for use in the paper industry. A column of granite was lathed and then drilled along its length, before the placement and tensioning of steel rods.
- In the 1980s, the General Post Office of Sydney underwent a restoration that used reinforcement by post-tensioning the sandstone clock tower. As a result of the reinforcement, Sydney GPO may be the first-ever post-tensioned stone building.
"A more than one hundred year old sandstone masonry building, … the GPO Tower will be strengthened with four vertical post-tensioning tendons, 19 diameter 0.5" strands each, and a number of horizontal prestressing bars diameter 35mm at floor levels. ... Special steel chairs will be used to anchor the tendons and spread the anchorage forces of 1,771 kN (400 kips). The anchorages of the unbonded tendons allow for monitoring and adjustment of the tendon forces to compensate volume changes of the sandstone, if necessary."[13]
- The first documented real-world use of post-tensioned stone in a new building was for the Pavilion of the Future, built in Seville for the Universal Exposition in 1992, designed by legendary structural engineer Peter Rice of Ove Arup and Partners.[7] Rice had worked on the Sydney Opera House, which was a major technical advance in part because of its use of pre-cast concrete masonry beams that were assembled into the roof superstructure using post-tensioning; this prior use of post-tensioned masonry may have contributed to Rice's use of post-tensioned stone decades later.
- Designed and constructed between 1991–2004, the arches of a 6000 sqm Sanctuary of Saint Pio of Pietrelcina by architect Renzo Piano and structural engineering led by Maurizio Milan of Favero & Milan engineers[18] and Arup Group.[19]
- Built in 1994, the 34 m-span Inachus footbridge in Oita, Japan uses post-tensioned stone, designed by engineer Mamoru Kawaguchi.[7] "The bridge has a lenticular shape with an arched upper chord and a suspended lower chord, connected to each other by means of web members consisting of steel tubes arranged to form inverted pyramids."
- Completed in 1995,[20] Queen's Building at Emmanuel College, Cambridge[7] by Hopkins Architects and Buro Happold[4] with Ove Arup and Partners.[21] "The columns were also used to provide lateral stability to the building and were post-tensioned using stainless steel rods attached directly to the foundations."[22]
- Completed in 1999, Punt da Suransuns in Switzerland, a 40 m footbridge[23] designed by civil engineer Jürg Conzett.
"Punt da Suransuns is a stress-ribbon bridge with a span of 40 m … constructed with slabs of Andeer granite, which are prestressed over rectangular steel bars … When traversing the bridge the vertical oscillation can be felt, but pedestrians have commented that the bridge is not as flexible as it looks."[24]
- Erected in 1999, Southwark Gateway Needle by Eric Parry is made of 25 blocks of Portland stone held 16m high by post-tensioning.[25][22][26]

PT stone in the early 2000s
- Completed in 2001, Portcullis House, a building of the UK Parliament, designed by Hopkins Architects.[4] This building represented a setback in PT stone, as the overall building was expensive.
- Completed in 2002, 30 Finsbury Square was completed by Eric Parry Architects [27][28] and Whitbybird engineers. "The columns were constructed conventionally and left to set for 7 days prior to post-tensioning.".[22]
- In 2004, Kusser Graniteworks constructed post-tensioned granite–diorite flagpoles.[29]
- In 2005, a prototype of the first post-tensioned spiral stone staircase was made; called "Escalier Ridolfi" it was designed by Claudio D'Amato and Giuseppe Fallacara.[30] In 2006, the full-scale Escalier Ridolfi staircase was presented at the Venice Biennale of Architecture, constructed by Ateliers Romeo stonemasons[31]
- In 2007, Kusser Granitwerke constructed their first tensioned stone footbridge, in Rosenheim.[32]
- Completed in 2009, a building on Southampton Row,[4] designed by Sheppard Robson architects, used post-tensioned stone.
PT stone in the 2010s
- Starting in 2011, award-winning high-tensile stone staircases for luxury residences were constructed through a collaboration between stonemason Pierre Bidaud and structural engineer Steve Webb,[33][16][34]
- In 2013, Giuseppe Fallacara and Marco Stigliano demonstrated the first "tensegrilithic" prototype, combining stone with steel rods and cables into a tensegrity structure.[35]
- From 2019, Webb Yates engineers used extended horizontal stone lintels in residential construction,[36] and proof-of-principle stone flooring panels.[37][3]
- A 330˚ helix staircase, designed by Foster and Partners for the 2019-completed Dolunay Villa in Turkey[38] and constructed by the Stonemasonry Company with Webb Yates.[39]
PT stone in the 2020s
- IABSE awarded the 2020 Milne Medal to Steve Webb for his work on developing low-carbon materials for structural engineering, including tensioned stone.[40]
- Due for completion in 2026, the Sagrada Familia cathedral under construction in Barcelona in partnership with the Arup Group uses post-tensioned stone assemblies.[12] "Jordi Faulí, the architect in charge of La Sagrada Familia in Barcelona, has stated that they will implement this technique for 800 panels that form part of the central towers of the basilica; in fact, prestressing will allow for a higher resistance to winds with less weight." Using post-tensioning allows the construction to avoid using stone-cladded concrete.[41]
See also

References
- ↑ Sebastian, Wendel; Webb, Steve (2021). "Tests on prototype pretensioned natural stone beams". Construction and Building Materials. 271: 121555. doi:10.1016/j.conbuildmat.2020.121555. S2CID 234318783.
- 1 2 Boote, Scott; Lynes, Alex (2020). "Stone as a structural material. Part 3: Post-tensioned stone structures". The Structural Engineer. 98 (8): 22–28. doi:10.56330/FZDA2725. S2CID 226721423.
- 1 2 3 4 5 6 Webb, Steve (2020). "Why the time is ripe for a return to stone as a structural material". The RIBA Journal. Retrieved 2023-05-02.
- 1 2 3 4 Bignell, Eric (2009). "Off-site manufacture : Post-tensioning".
- 1 2 Groupwork; Jackson Coles; Eight Associates; Webb Yates; The Stonemasonry Company; Polycor (2020). "Stone Tower Research Project" (PDF). The Building Centre.
- ↑ "The pros and cons of stone buildings". Financial Times. 17 June 2022.
- 1 2 3 4 5 6 Todisco, Leonardo; Stocks, Elizabeth; León, Javier; Corres, Hugo (2018). "Enhancing the Structural Performance of Masonry Structures by Post-Tensioning". Nexus Network Journal. 20 (3): 671–691. doi:10.1007/s00004-018-0374-z. S2CID 253601720.
- ↑ "The New Stone Age | Exhibitions | What's on | Building Centre".
- ↑ Simpson, James (2020). "Stone & lime in post-modern construction: Climate change and a new stone age".
- ↑ Webb, Steve (2022). "Stone age: a new architecture from an old material". The Architectural Review. Retrieved 2023-05-02.
- ↑ "Tensioned-stone panels: Structure and components". 22 August 2018.
- 1 2 "Tensioned stone". 6 June 2018.
- 1 2 Ganz, Hans Rudolf (1988). "POST-TENSIONED MASONRY STRUCTURES" (PDF). structural technologies. VSL INTERNATIONAL LTD.
- ↑ Reinforced and prestressed masonry. 1982. doi:10.1680/rapm.01619. ISBN 978-0-7277-4902-4.
- ↑ https://www.pure.ed.ac.uk/ws/portalfiles/portal/5952527/R_pedreschi_post_tensioned_stone.pdf
- 1 2 https://www.stoneshow.co.uk/stone-digital-conference/innovation-for-sustainable-design-back-to-basics-post-tensioned-stone-and-lightweight-fa%C3%A7ades
- 1 2 Donaldson, Barry (1988). New Stone Technology, Design, and Construction for Exterior Wall Systems. ASTM International. ISBN 9780803111646.
- ↑ "Padre Pio Pilgrimage Church / Renzo Piano Building Workshop". 27 August 2018.
- ↑ https://arquitecturaviva.com/works/iglesia-de-peregrinacion-padre-pio-san-giovanni-rotondo-0
- ↑ "Queen's Building, Emmanuel College Cambridge – Education – Hopkins Architects".
- ↑ https://www.archinform.net/projekte/4999.htm
- 1 2 3 Pedreschi, Remo (2013). "A feasibility study of post-tensioned stone for cladding". Construction and Building Materials. 43: 225–232. doi:10.1016/j.conbuildmat.2013.02.008. S2CID 55570473.
- ↑ https://www.researchgate.net/figure/Segmented-post-tensioned-bridges-a-Punt-da-Suransuns-J-Conzett-Switzerland-b_fig3_362652352
- ↑ Conzett, Jürg (2000). "Punt da Suransuns Pedestrian Bridge, Switzerland". Structural Engineering International. 10 (2): 104–106. doi:10.2749/101686600780557965. S2CID 109661483.
- ↑ "Southwark Gateway Needle".
- ↑ "Southwark Gateway Needle by Eric Parry Architects (1999)".
- ↑ "30 Finsbury Square: Perspective looking northeast | Works of Art | RA Collection | Royal Academy of Arts".
- ↑ "30 Finsbury Square".
- ↑ https://kusserusa.com/portfolio/vorgespannte-fahnenmasten
- ↑ "Pietre d'Italia".
- ↑ "FIRST post-tensionned staircase in massive stone".
- ↑ "Footbridge in Rosenheim".
- ↑ "Post Tensioned and Reinforced".
- ↑ "See the Engineering Behind This Floating, Award-Winning Stone Helical Stair". 22 November 2016.
- ↑ http://www.atelierfallacara.it/_download/Monografie/21_Architectural_stone_elements.pdf
- ↑ "Why build with concrete when you can build with stone?".
- ↑ "From Field to Form: Stone".
- ↑ "Dolunay Villa / Foster + Partners". 30 March 2020.
- ↑ "Private Villa".
- ↑ https://www.istructe.org/resources/training/iabse-milne-medal-lecture-2020/
- ↑ https://blog.sagradafamilia.org/en/specialists/the-stones-for-the-central-towers/